Nowadays, the demand for faster and smaller electrical devices is more than ever before. As a result, the electronics industry uses Surface Mount Technology (SMT) to directly complete and solder electronic elements onto the surface of printed circuit boards. For SMT components with small or no leads, solder paste and reflow soldering specify electrical connections.
Let’s start with the basics. What is surface mount technology? Basically, it is a method for assembling electronic components directly onto the surface of a printed circuit board (PCB). SMT, developed in the 1960s and 1970s, replaced conventional through-hole technology, producing more compact, economical, and efficient electronic devices.
According to stats, the surface mount technology (SMT) equipment market is valued at $5.73 billion and is expected to grow at a CAGR of 11.5% from 2024 to 2031. Read on to know everything about Surface Mount Technology (SMT), including its features, use cases, types, and benefits.
Key Highlights
- Surface Mount Technology (SMT) is a method for assembling electronic components directly onto the surface of a printed circuit board.
- THT creates larger PCBs while SMT can facilitate miniaturisation of electronic devices.
- As compared to THT, SMT has cheaper production costs, increased component density, and superior electrical performance. But the initial cost is high and it is difficult to repair.
- SMT is used in many industries like consumer electronics, medical, and aerospace industries.
- The two main soldering techniques are reflow soldering and wave soldering.
- Assembling PCBs using SMT involves various steps like solder paste application, component placement, reflow soldering, and cleaning.
The Development of Surface Mount Technology (SMT)
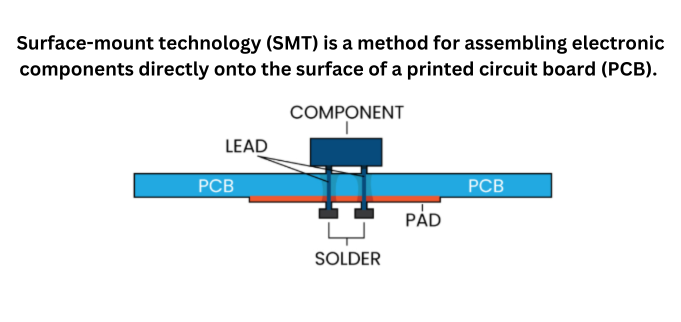
Since its introduction, Surface Mount Technology (SMT) has accomplished some important milestones. The need for increasingly compact and effective electrical devices propelled the development of SMT. Improved performance, lower costs, and a higher component density utilised the transition from through-hole technology to SMT.
Important changes, including the introduction of automated assembly procedures and improved soldering techniques, have greatly impacted electronic manufacturing. These advancements increase productivity, lower labour costs, and improve the reliability of contemporary electronic devices, especially in detailed PCB layers where accuracy and efficiency are necessary.
Key Features of Surface Mount Technology
Several key features of Surface Mount Technology (SMT) improve electronic manufacturing.
- The PCB surface is directly attached to the components, negating the need for drilled holes. This method allows for the use of smaller components than through-hole technology, making denser circuitry possible.
- The high level of automation in the assembly process shortens manufacturing times and decreases expenses.
- Due to the small components and lack of drilled holes, SMT also results in lighter and smaller PCBs. Modern electronic devices prefer SMT because it improves electrical performance by reducing parasitic effects and shortening signal routes.
Differences Between Through-Hole Technology and Surface Mount Technology
Through-Hole is yet another technology in electronic manufacturing that focuses on assembling electronic components onto printed circuit boards (PCBs) by inserting the leads of components through holes drilled into the board. Check out the key differences between THT and SMT:
Factors to Consider When Choosing SMT or Through-Hole Technology
When deciding between Surface Mount Technology (SMT) and Through-Hole Technology (THT), manufacturers must consider various factors like cost, application, performance requirements, and limitations in production.
SMT has cheaper production costs, increased component density, and superior electrical performance. This makes it perfect for small, powerful devices like laptops and smartphones.
Since through-hole technology offers better mechanical bonding, it is ideal for high-stress applications like those in the automotive and aerospace industries.
Pros and Cons of Surface Mount Technology
Pros
- Surface Mount Technology (SMT) offers multiple benefits in electronics manufacturing.
- For higher component density, smaller PCB components, and better electrical performance.
- The automated assembly technique decreases both production time and costs.
Cons
- Smaller PCB components can be challenging to manage and fix, and the technology is less appropriate for high-stress settings where strong mechanical bonding is needed.
- The initial investment required for SMT is higher, which could be beyond the reach of many companies.
Optimal Use Cases for Surface Mount Technology
The comprehensive set of features of SMT makes it a perfect choice in many industries like:
- Consumer Electronics: Surface Mount Technology (SMT) is extremely useful in consumer electronics, such as smartphones, laptops, and wearables, since it offers compact, lightweight designs and high component density on PCBs.
- Medical Industry: SMT helps the medical industry build portable equipment such as pacemakers and glucose monitors. Infotainment systems and advanced driver assistance systems (ADAS) are two examples of automotive uses. In addition, SMT makes it possible to miniaturise medical implants and portable diagnostic instruments.
- Aerospace Industry: Due to technological improvements in automation and miniaturisation, SMT is a safe choice for creating effective lightweight aerospace equipment.
SMT's appropriateness for these complex uses is guaranteed by its capacity to manage fast production lines without sacrificing quality.
Best Practices for SMT Component Placement
- Use strategic layout designs, maintain appropriate spacing, and align orientations accurately to achieve optimal SMT component placement on PCBs.
- Regular issues such as overpopulation and misalignment can be avoided by following the standards.
- Properly placed PCB components improve performance, reliability, and manufacturing efficiency, which is important for devices such as cell phones and medical equipment.
Soldering Techniques in Surface Mount Technology
Standard SMT soldering techniques include reflow and wave soldering.
- Reflow Soldering: it is the technique of applying solder paste to PCB components and arranging them on the board. Finally, they are passed through a reflow oven. Although it needs expensive equipment, this method guarantees uniform heating and exact control.
- Wave soldering: it is appropriate for mixed technology boards that involves passing the PCB across a hot solder wave. It works well for simpler assemblies because it is less efficient and more affordable. Both technologies depend on proper setup, temperature management, and flux application to produce dependable connections and high-quality PCB components.
Types of Surface Mount Device Packages
- Basic SMT: The components of this kind of PCB assembly are put on one or both sides of the board. Since special tools are not needed for this kind of surface mount, it is easy to use.
- Advanced SMT: More sophisticated gadgets will have this kind of technology. It combines the technologies of through-hole and surface mount. SMT and through-hole assembly are both present on the primary side of PCb, whereas SMT is the only assembly type on the other. When you require additional components on a single-sided PCB, this approach works well. At this instance, the electrical function is likewise superior.
- Versatile SMT: In this type, the main side of the board has a through hole. However, soldering and components are present on both sides. As stated otherwise, it is an alternative method of advanced assembly.
Measuring Surface Mount Device Sizes
Accurate measurement is critical for ensuring that PCB components fit and work properly. Using defined identifiers like 1812, 1206, 0805, 0603, 0402, and 0201 which indicate dimensions in hundredths of an inch—makes measuring and categorising Surface Mount Device (SMD) sizes easier. While passive SMDs like resistors and capacitors use these size codes, diodes and transistors use package styles to determine orientation. Integrated circuits are classified into several categories, ranging from BGA for complex VLSI processors to SOIC for basic devices. Accurate measurement in electronic assemblies provides stable connections and maximum performance.
Designing for Surface Mount Technology
1. Arrangement Points
- Assemble parts close to reduce unwanted inductance and spurious capacitance.
- To increase the density of PCB components, use a compact layout.
- For the best design, adhere to IPC-7351 requirements.
2. Selection of Components
- Because SMT parts dissipate less power, choose components with appropriate power ratings.
- For exact power and performance statistics, see the manufacturer's data.
- Verify that the components are compatible with SMT assembly procedures.
3. Temperature Control
- Use heat sinks and thermal vias to control heat dissipation.
- Provide enough ventilation around high-power components in the design.
- Make use of coatings and materials that improve thermal conductivity.
4. Standards and Design Guidelines
- Observe industry standards such as IPC-7351 with regard to positioning and footprint specifications.
- Verify that the PCB pad designs are attached to the manufacturing specifications.
- Use prototyping and simulation to validate the design to ensure it can be manufactured.
Assembling PCBs Using Surface Mount Technology
Do you know that most parts in the iPhone 14 were most likely manufactured using surface mount technology (SMT)? Many parts in your modern car or Uber trip were assembled using SMT technology.
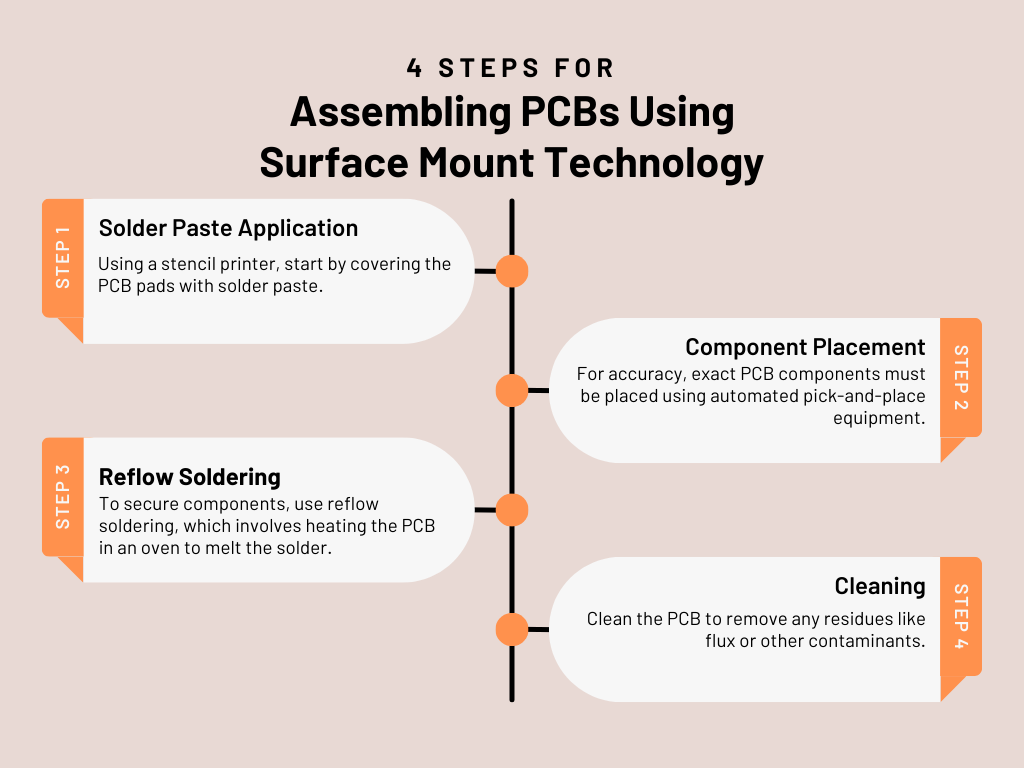
1) SMT-Based PCB Assembly Process
- Using a PCB stencil printer, start by covering the pads with solder paste.
- For accuracy, exact PCB components must be placed using automated pick-and-place equipment.
- To secure components, use reflow soldering, which involves heating the PCB in an oven to melt the solder.
- Clean the PCB to remove any residues like flux or other contaminants.
2) Tools and Methods
- Make use of reflow ovens, pick-and-place devices, and solder paste printers.
- For quality control, use inspection instruments such as Automated Optical Inspection (AOI).
3) Tricks and Difficulties for Troubleshooting
- To rectify soldering flaws, modify oven temperature profiles.
- Make sure all the parts are aligned correctly to prevent mistakes in placement.
- Maintain and sanitise equipment on a regular basis to avoid faults.
Managing Board Expansion and Flexure in SMT
Board expansion and flexure in SMT can cause mechanical stress and thermal cycling problems, reducing the dependability of PCB components. Expanding and contracting due to thermal cycling might result in solder joint failures. Board flexure can cause mechanical stress and damage to fragile SMT components.
To avoid these problems, utilise materials with matching thermal coefficients to reduce differential expansion. To minimise flexure, design boards with adequate thickness and support structures. To effectively dissipate heat, use correct thermal management techniques like heat sinks and thermal vias. Maintaining these tactics aids in maintaining the performance and integrity of SMT assemblies.
Applications of Surface Mount Technology
- As electronic gadgets get smaller and more complex, SMT technology has become more and more prevalent.
- It is a great option for producers who want to create gadgets that are small, powerful, and affordable.
- SMT components are frequently found in home automation system foundational devices including security cameras, doorbells, and smart thermostats because of their small size and effective construction.
- Numerous industries heavily rely on the SMT Assembly process, including consumer electronics, telephony, and industrial IoT.
- Manufacturers can decrease the overall size of the gadget while preserving or enhancing its performance by employing SMT technology.
Cost Benefits of Surface Mount Technology
SMT components are cost-effective, considering their benefits. Smaller components are used in SMT, which maximises PCB space. SMT automation lowers the amount of manual labour required, lowering production costs and boosting consistency.
The assembly procedure is streamlined by the ability to mount components on both sides of the PCB. It requires drilling, bigger parts, and hand insertion, which raises the cost of labour and materials. It reduces overall costs by doing away with the necessity for drilling, enabling automated assembly, and speeding up manufacturing.
Above all, SMT lowers board size and material costs by enabling higher density and smaller components.
Key Characteristics of Surface Mount Technology
- Surface Mount Technology (SMT) uses PCB components attached directly to the board's surface, avoiding the requirement for drilled holes.
- SMT provides lower production costs, better performance, and increased component density.
- It increases automation and efficiency by using solder paste printing to securely insert components.
- SMT components allow for lightweight and compact designs since they are available in various forms and sizes, including resistors, capacitors, diodes, and integrated circuits.
- Smartphones, medical equipment, and automotive systems are examples of real-world applications where SMT's dependability and miniaturisation potential are important.
Important Considerations in Surface Mount Technology
- When applying Surface Mount Technology (SMT), think about material selection, PCB component layout, and process control.
- To guarantee performance and longevity, choose premium materials. The best possible component spacing, heat management, and signal interference reduction should all be taken into account during design.
- Efficiency depends on precise process control. Throughout the assembly process, routine testing and inspections can assist in identifying and reducing possible problems.
- Following industry standards and best practices will allow dependable and efficient SMT implementation, improving PCB components' performance and longevity.
Conclusion: The Future of Surface Mount Technology
It is reasonable to wonder how SMT technology will develop to satisfy growing industry demands given its long history and the numerous adjustments it has undergone as PCB assembly demands have grown. Concerns about the environmental sustainability of SMT projects have become one of the most common ones regarding PCB assemblies in recent years. RoHS compatible solder has required modifications to SMT procedures as this technology continues to adapt to new industry standards. Apart from utilising lead-free solder, PCB producers and assemblers will persist in satisfying their clientele by utilising developing SMT technologies.