A solder mask layer is an important protective layer that is put on a printed circuit board (PCB) during production. It works like a thin lacquer on top of the copper traces on the PCB to keep solder from spreading to places it's not supposed to go during the soldering process. The solder mask's main job is to stop short circuits, rust, and other damage that could make the board less useful.
The solder mask makes sure that only the designated areas are soldered, like pads and vias by protecting and insulating the uncovered copper. This layer helps the PCB last longer and be more sturdy by protecting the circuit from things like dust and moisture. Basically, it is very important to keep the integrity and reliability of the electrical connections on the board so that the PCB always works as it should. Check out all you need to know about the importance of solder mask and its usage.
Key Highlights
- A solder mask is a secure covering that must be put on printed circuit boards (PCBs) in order for them to work and last.
- You must make sure that there is enough solder mask clearance, bridge width, expansion, and openings.
- The different types of solder masks are: epoxy-based solder mask, Liquid Photoimageable solder mask, dry film solder mask, and top-side and bottom-side solder mask.
- A solder mask is a permanent protective layer to stop solder from bridging inadvertent areas while a paste mask is the pattern designed for surface-mount assembly process.
- Solder mask protects the exposed parts of PCB, offers electrical insulation between several conductive portions, and helps in circuit identification.
What Is a Solder Mask and Why Is It Essential?
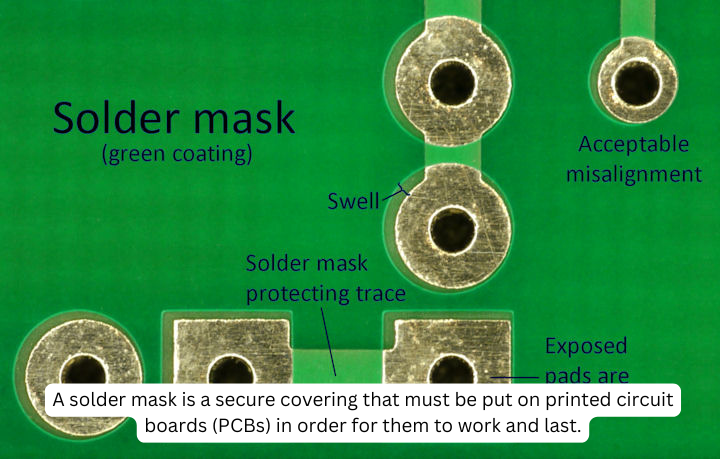
A solder mask is a secure covering that must be put on printed circuit boards (PCBs) in order for them to work and last. That's because it forms a barrier over most of the copper traces on the PCB, leaving only pads and vias which can be soldered. A solder mask's main job is to stop solder bridges, which are connections made by mistake with extra solder between two or more nearby electrical contacts. These bridges can cause short circuits that make the circuit less safe and less effective.
The solder mask has other important benefits besides preventing solder bridges. It keeps the PCB safe from things like chemicals that can damage or corrode the copper lines, dust, and water. Insulating the PCB also lowers the chance of oxidation, which guarantees the electrical stability of the board for life. The solder mask also acts as a barrier against heat, which makes thermal control better.
Using a solder shield is an important part of designing circuit boards because it protects the boards during the soldering process and also makes the boards more reliable in their normal use. It makes sure that the solder joints are better and more accurate, lowers the risk of short circuits, and makes the machine more stable in general. These traits make the solder mask an important part of modern PCB production, especially as circuit designs get smaller and more complicated.
Key Design Guidelines for Solder Mask Design
Printed circuit boards (PCBs) depend on the solder mask layer that is meant to make them reliable and easy to make. To get the best performance and production efficiency, you should follow the Design for Manufacturability (DFM) rules. The following are four important DFM rules for making solder masks and how they improve the general production and trustworthiness of PCBs.
1. Solder Mask Clearance
The first major rule is to make sure there is enough solder mask clearance, which is the space between pads and vias that are made of copper that can be seen. By clearly defining this distance, pad coverage can be avoided by accident. To account for differences in how things are made, the clearance should generally be a few mils bigger than the pad size.
A good solder mask space makes sure that the solder can wet the pads properly, which makes it possible for strong and reliable solder joints. Too much room makes short circuits more likely because copper is exposed, but not enough space could mean that the mask over the pad doesn't fully cover weak joints. This rule is important for high-yield manufacturing as it lowers the chance of mistakes and makes sure that the boards are reliable.
2. Solder Mask Bridge Width
The small part of the mask that is between two pads is called the solder mask bridge. For example, solder mask bridge thickness becomes very important on fine-pitch parts. If the bridge is too small, it might print wrong during production, which could lead to solder bridges and short circuits between pads that are close together.
On the other hand, a bridge that is too big could make it hard to get to the pads while soldering. To make sure the mask is applied correctly, designers should follow the minimum bridge width suggestions made by the maker. Not only does this keep electrical shorts from happening, but it also makes the PCB stronger and last longer by isolating active areas properly.
3. Solder Mask Expansion for Vias
Another very important rule is to use solder mask extension for vias. With vias, which connect different layers of the PCB, you can leave them open or cover them with a solder mask. There are two types of vias: "tented" and "untented." With "tented" vias, the solder mask extends over the via, making it closed.
When tenting is used, it is very important that the solder mask goes a little beyond the edge of the through-hole to avoid production errors. If you do the right amount of expansion, you can avoid problems like solder leaking into the via hole, which could cause nearby components to have defective solder joints. This rule makes the solder mask layer more reliable, which lowers the chance that it will fail because of bad soldering or contamination.
4. Defined Solder Mask Openings for SMD Pads
For surface-mount devices (SMD), accurately describing the solder mask apertures is necessary for the correct soldering of the parts. For example, for BGA (Ball Grid Array) packages, the solder balls must make good contact with the PCB, which means that the solder mask holes must be correct. If the cover holes are too big, solder could overflow and possibly bridge between the pads.
On the other hand, holes that are too small could make it hard to solder, which would lead to weak links. By following the manufacturer's instructions for solder mask opening sizes, makers can be sure of strong solder joints, which will make the board more reliable and last longer.
Types of Solder Masks and Their Applications
Designed to prevent solder bridges, shield copper traces, and improve the general board longevity, solder masks are crucial protective PCB layers used in manufacture. There are several kinds of solder masks with different qualities, uses, and benefits. We investigate the several varieties of solder masks here, contrasting their features and applications.
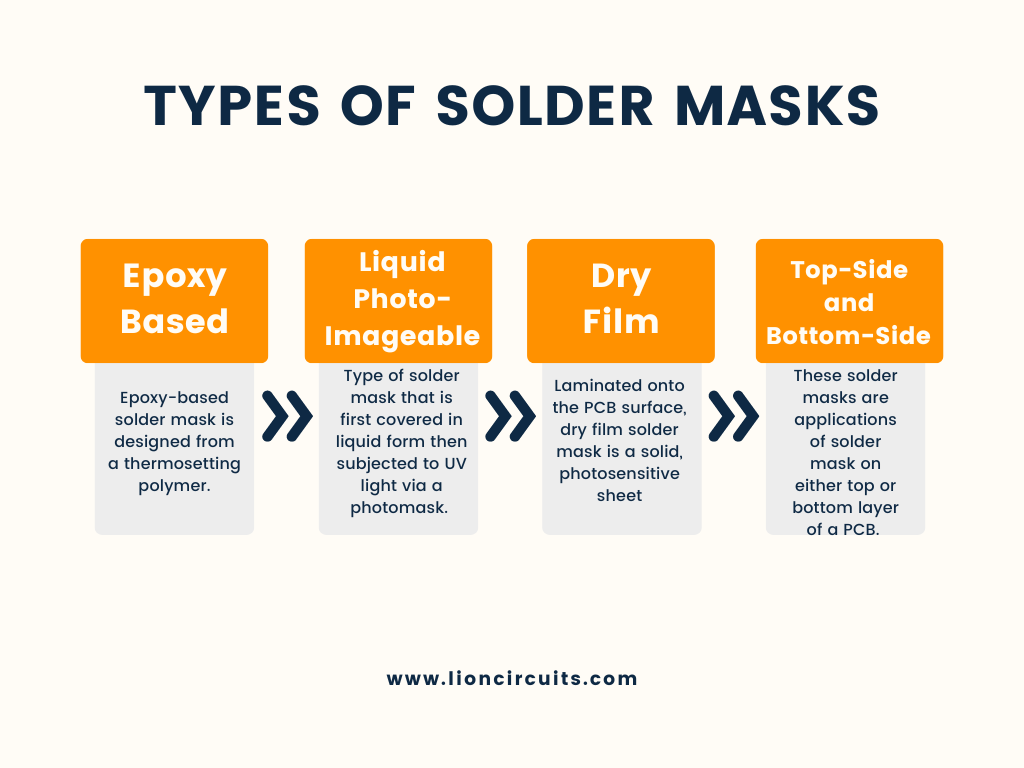
1. Epoxy-Based Solder Mask
Designed from a thermosetting polymer, epoxy-based solder mask is among the most conventional forms. Usually screen printed onto the PCB, this kind of mask is then thermal-cured. Because of their low cost and simplicity of application, epoxy solder masks are extensively utilised and fit for simpler, low-cost PCB designs.
Properties and Advantages:
- Cost-effective: Epoxy-based masks are among the least expensive options, making them attractive for basic or low-volume production runs.
- Good Insulation: They provide decent electrical insulation and protection against contaminants.
- Simple Application: The screen-printing method is easy to apply and suitable for less complex boards.
Uses:
- Commonly used in consumer electronics and low-cost, low-performance PCBs.
- Suitable for single-sided PCBs and boards with fewer precision requirements.
However, epoxy-based solder masks tend to have lower resolution and durability compared to other types, making them less ideal for advanced, high-density PCB designs.
2. Liquid Photo-Imageable (LPI) Solder Mask
Modern PCB manufacture makes greatest use of liquid photo-imageable (LPI) solder masks. The PCB is first covered in liquid form then subjected to UV light via a photomask. Whereas the unexposed portions are eliminated, the exposed areas harden. This enables quite exact and high-resolution applications.
Properties and Advantages:
- High Precision: LPI solder masks are capable of producing fine details and sharp edges, making them ideal for high-density, complex PCB designs.
- Variety of Colors: LPI masks are available in various colours, including green, blue, black, and white, allowing for customization.
- Good Adhesion and Durability: LPI masks offer excellent adhesion to the PCB surface and provide robust protection against environmental factors.
Uses:
- Predominantly used in high-performance and high-density PCBs, such as those found in telecommunications, medical devices, and aerospace applications.
- Suitable for multi-layer boards, where precision is critical.
LPI masks are more expensive than epoxy-based masks, but their precision and durability make them the preferred choice for most modern PCB applications.
3. Dry Film Solder Mask
Laminated onto the PCB surface, dry film solder mask is a solid, photosensitive sheet. It is then developed to eliminate unexposed portions by UV light passing through a photomask, much as in the LPI process. Excellent resolution and thickness control of this kind of solder mask are well-known.
Properties and Advantages:
- High Resolution: Like LPI masks, dry film masks allow for precise control, making them suitable for intricate and fine-pitch designs.
- Thickness Control: The thickness of the mask can be easily controlled, offering greater flexibility in design.
Uses:
- Often used in advanced applications where precision is essential, such as high-frequency circuits and multilayer PCBs.
- Preferred for boards with high-density BGA (Ball Grid Array) and fine-pitch components.
Dry film solder masks can be more expensive and complex to apply, but they are valued in high-end applications where precision and uniformity are critical.
4. Top-Side and Bottom-Side Solder Mask
Top-side and bottom-side solder masks are applications of solder mask on either top or bottom layer of a PCB. These kinds point to where the solder mask is applied rather than different materials.
Properties and Advantages:
- Protection on Multiple Layers: By applying solder masks to both the top and bottom sides, the entire PCB is protected from contaminants and solder bridging.
Uses:
- Suitable for double-sided boards where both sides have copper traces and components.
Standard Thicknesses for Solder Mask Layers
Solder mask layers usually range in standard thickness from 0.7 mils to 1.5 mils (18 to 38 microns). For most printed circuit boards (PCBs), this range is regarded as optimal since it strikes a compromise between manufacture and protection. The type of solder mask used—liquid photo-imageable (LPI) or dry film—as well as the particular PCB design requirements usually help to define the thickness.
Impact of Thickness on PCB Performance and Durability
The general PCB performance and longevity depend much on the thickness of the solder mask. Better protection against elements such moisture, dust, and chemicals—which can corrode copper traces or compromise the circuit's operation—that thinner solder mask layers provide helps prevent This further protection extends the lifetime of the PCB, especially in demanding surroundings where exposure to such components is somewhat frequent. Though it increases endurance, a thicker solder mask might also have negative effects. Particularly with fine-pitch components, an excessively thick solder mask could cause alignment problems during the production process. Moreover, excessive thickness can make it more difficult for the solder to adequately wet the PCB pads, therefore producing either weak or partial solder junctions. Conversely, a too thin solder mask could not be able to offer enough insulation and protection, therefore raising the possibility of solder bridges, shorts, and corrosion.
IPC-SM-840 Standards for Solder Masks
The generally accepted guideline controlling solder mask performance and quality in printed circuit board (PCB) manufacture is the IPC-SM-840 standard. Designed by the Institute for Printed Circuits (IPC), this standard specifies solder mask materials' standards for durability, performance, and environmental protection, therefore guaranteeing that they satisfy rigorous requirements. Important areas including adhesion, hardness, insulating resistance, flammability, moisture and solvent resistance are covered by the IPC-SM-840 standard.
Key Criteria of IPC-SM-840 Standards
- Adhesion: Strong adherence of solder masks to the PCB surface helps to prevent delamination under mechanical stress and thermal cycling. This guarantees the solder mask remains whole during the PCBs lifetime.
- Insulation Resistance: Under high-voltage or high-frequency situations especially, the standard requires solder masks to retain high insulation resistance to prevent electrical shorts between adjacent traces or components.
- Flammability: Solder masks have to satisfy particular flammability criteria to lower the running fire danger.
- Moisture and Solvent Resistance: Maintaining the integrity of the PCB in humid or chemically hostile conditions depends on solder mask resistance against moisture absorption and solvent exposure being guaranteed by the IPC-SM-840 standard.
- Thermal Resistance: The solder mask should resist high temperatures in the operational environment of the board and during soldering, therefore preventing discoloration or degradation.
Benefits of Adhering to IPC-SM-840 Standards
Maintaining the long-term dependability and performance of PCBs depends on manufacturers following the IPC-SM-840 guidelines. Following these guidelines will help manufacturers make sure the solder mask resists environmental stresses, stops short circuits, and offers sufficient protection. This compliance increases consumer confidence, stretches the lifetime of the product, and lessens the possibility of board failures. These criteria eventually help PCBs to be more manufacturable and to have quality assurance, so producing consistent and dependable product performance.
The Application Process: How Solder Mask Is Applied
In printed circuit board (PCB) manufacture, solder mask application is a crucial step guaranteeing the board's durability and correct performance. Two main techniques of putting solder masks are photo imaging and screen printing.
1. Screen Printing
For simpler PCB designs, a conventional technique utilised mostly is screen printing. This procedure pushes an epoxy-based solder mask across a stencil or mesh screen onto the surface of the PCB. Heat application then cures the mask. Although this approach is quite affordable, it is best suited for low-precision uses since screen printing makes it difficult to attain homogeneous thickness or fine features.
Importance:
For simpler, less expensive boards where great accuracy and uniformity are not as important, screen printing is perfect. Modern high-density PCB manufacturing does not extensively use it, nevertheless, owing to its restrictions in precision and control over the mask's thickness.
2. Photo Imaging
Modern PCB manufacturers most commonly use photo imaging, most especially Liquid Photo-Imageable (LPI) solder masks. This procedure starts by liquid photo-imageable substance coating the PCB. The assembly is then subjected to ultraviolet (UV) radiation after a photomask with the intended design is laid across the board. While the unexposed sections are wiped away and a precise mask pattern results, the exposed areas solidify. The board is next cured to complete the layer of solder mask.
Importance: For complicated, high-density PCBs, photo imaging is perfect since it lets one achieve great accuracy. Important for preventing solder bridges, enhancing insulation, and shielding copper traces from environmental pollutants, the technique guarantees homogeneity in solder mask thickness. It also enables high performance uses and fine-pitch components.
Understanding Peelable Solder Masks
Applied to certain sections of a printed circuit board (PCB) during production, peelable solder masks are transient protective coatings. Peelable masks, unlike conventional solder masks—which are permanent—are meant to be taken off when soldering is finished. Usually used over locations needing temporary protection—gold-plated contacts, vias, or specialised pads meant to remain solder-free during wave or reflow soldering operations.
They are thicker than conventional solder masks, the peelable mask material can survive high temperatures, which qualifies for shielding delicate sections during the heat-intensive soldering operation. The peelable mask is manually removed once soldering is complete to expose the protected areas—such as test points or connectors.
Key Differences and Benefits:
- Temporary vs. Permanent: Peelable solder masks provide temporary protection, whereas standard masks are permanent.
- Specific Applications: Peelable masks are used for selective protection during soldering, ideal for areas needing later access or further processing.
- Benefits: They prevent solder from sticking to areas where it is not desired, thus enhancing production flexibility and preventing damage to sensitive parts of the PCB.
Solder Resist vs. Paste Mask: Key Differences
Although they are used at various phases of assembly and have different uses, solder resist—also known as solder mask—and paste masks are both absolutely vital in printed circuit board (PCB) manufacture.
Solder Resist (Solder Mask)
Applied to the PCBs surface, solder resist—also known as solder mask—is a permanent protective layer. Its main purpose is to stop solder from bridging inadvertent areas—especially between copper traces, pads, and vias—during the soldering process Additionally serving as an insulator, the solder mask shields the PCB from environmental pollutants like dust, moisture, oxidation, and other impurities. The solder mask's covered sections will not be soldered; only the specified areas—such as pads and vias—will receive solder.
Applications:
- Solder resist is used on the PCBs surface to insulate copper traces and prevent accidental solder connections.
- It provides long-term protection for the PCB from environmental factors, ensuring durability and electrical integrity.
Paste Mask
A paste mask, sometimes known as a stencil, is the pattern designed for surface-mount assembly process solder paste application. Solder paste is applied exactly onto the pads where surface-mount devices (SMDs) will be mounted. To enable the component placement and soldering during reflow soldering, the paste mask specifies the precise sites where solder paste should be put. The paste mask is only temporary and utilised just during the assembly process unlike the solder mask.
Applications:
- Paste masks are employed during the assembly phase to accurately apply solder paste to the designated pads for SMDs.
- They ensure the correct amount of solder paste is applied for proper component placement and soldering.
Key Differences:
- Function: Whereas the paste mask regulates the application of solder paste during assembly, solder resist shields the PCB from soldering mistakes and environmental damage.
- Permanence: Whereas the paste mask is a temporary tool used just during component placement and soldering, solder resist is a permanent layer on the PCB.
- Stage of Use: Solder resist is utilised throughout the PCB manufacturing process; the paste mask is used subsequently during surface-mount assembly.
How To Manage Solder Mask Defects: Common Issues and Solutions
Reliability and performance of printed circuit boards (PCBs) depend on the solder mask flaws being managed. Typical flaws in solder masks are slivers, inadequate covering, registration problems, and air bubbles. These flaws could jeopardise the board's performance, causing short circuits, inadequate insulation, or perhaps board failure. Here are typical problems with reasonable fixes for controlling them:
1. Slivers
Issue: Thin, undesired bits of solder mask known as slivers linger between pads or traces from incorrect mask removal or misalignment during manufacture. They could create short circuits or compromise the electrical performance.
Solution: The best way to avoid slivers is to guarantee correct alignment throughout the photo imaging process and keep the appropriate clearance between pads and traces. Regular inspections and correctly calibrated photomasks help to reduce slivers risk.
2. Incomplete Coverage
Issue: When areas of the PCB are exposed because of unequal application or inadequate material, incomplete solder mask coverage results. This compromises the board's lifetime by leaving copper traces sensitive to oxidation and corrosion.
Solution: To get consistent coverage, carefully change the application settings including thickness and exposure levels. Frequent production-based inspections and tests help to find locations where covering is inadequate, therefore enabling adjustments before ultimate curing.
3. Registration Issues
Issue: Misaligned solder masks can cause incorrect PCB protection, either leaving vital sections covered or exposing them to solder. Often this results from improper photomask alignment.
Solution: Use exact registration controls throughout the photo imaging process to guarantee the solder mask lines up properly with the copper features. Consistent quality checks and routine equipment calibration help to prevent misalignment.
4. Air Bubbles
Issue: Particularly during thermal cycling, air bubbles caught under the solder mask during application might produce weak areas that might eventually peel or delaminate.
Solution: Make sure the solder mask is evenly and smoothly applied using enough drying and curing times. During application, controlled conditions or vacuum systems can assist to eliminate air bubbles.
Solder Mask Design Considerations and Best Practices
Reliability and functionality of a printed circuit board (PCB) depend on a solder mask being designed effectively. Throughout the design process, several factors—including alignment, coverage, and compatibility with other PCB components—must be addressed. Following best standards can help manufacturers create exact, dependable solder mask designs that increase PCB performance and lifetime.
Key Considerations:
- Alignment: solder mask must be precisely aligned with copper features. Any alignment can provide either covered or exposed copper pads, which causes soldering problems or short circuits. To prevent mistakes during the soldering operation, designers should make sure the solder mask openings exactly line the component pads and vias.
- Coverage: Protection of the copper traces from oxidation, moisture, and impurities depends on appropriate solder mask covering. For all locations except where solder joints are needed—such as pads and vias—designers should indicate solder mask coverage. While insufficient coverage may expose copper to ambient elements, hence increasing the danger of corrosion, overlapping solder masks might result in weak solder connections.
- Compatibility: The solder mask material has to be fit for the components and assembly technique of the PCB. It ought to resist chemical and cleaning agent exposure as well as high temperatures during soldering. Long-term dependability depends mostly on ensuring compatibility with the thermal requirements and material qualities of the board.
Best Practices:
- Define Clearance and Expansion: Keep appropriate clearance around vias and pads to permit enough solder mask expansion. This keeps protection for adjacent traces while helping to prevent inadvertent mask covering of solderable locations.
- Reduce Solder Mask Bridges: Make that solder mask bridges—narrow gaps between pads—are big enough to be consistently printed throughout manufacturing, therefore preventing mechanical instability and avoiding electrical shorts.
- Use Appropriate Thickness: Choose the proper thickness. Create the solder mask with a thickness suitable for balancing manufacturing ease with protection. Though they provide more protection, thicker PCB layers may cause fine-pitch designs to line incorrectly.
How to Incorporate Solder Mask into PCB Designs
Ensuring the board's manufacturability, dependability, and performance depends on including solder mask considerations throughout the PCB design process. Designing with a solder mask in mind means organising for coverage, clearances, and layer standards that fit the board's functionality and PCB assembly criteria.
1. Solder Mask in Design Phase
The designer has to specify the places where solder mask should or shouldn't be used during the PCB design stage. This usually includes deciding which parts of the board—such as pads, vias, and components—should be left uncovered for soldering. The solder mask will guard the copper traces against oxidation, solder bridging, and environmental degradation in the other locations.
Considerations include:
- Clearance and Expansion: Specify suitable solder mask clearance around vias and pads to stop the mask from invading solderable regions. The design should include this clearance to provide best mask alignment during production.
- Assignments for Layering: Make sure the solder mask layer corresponds to the suitable layers found in the design tool. Clearly marking these layers will help to prevent manufacturing confusion.
2. Integrating Solder Mask into Design Files
Manufacturers employ design files using Gerber or ODB++ forms, which incorporate solder mask parameters, to create the PCB. Usually shown as a negative image in the design software, the solder mask layer represents cutouts for the exposed areas—like pads. Add the solder mask layer together with other important PCB layers including copper, silkscreen, and drill data while creating design files.
3. Alignment with Schematics
Although the PCB layout stage defines most solder mask elements, designers should make sure early in the schematic design any components needing specific mask treatments—such as exposed test points or tented vias—are found. By use of design comments or layer designations in the schematics, expressing these needs facilitates the manufacturing process.
Important Functions of a Solder Mask
Improving the lifetime, dependability, and functionality of printed circuit boards (PCBs) depends on the solder mask in numerous important ways. These are its main purposes:
1. Protection
The solder mask shields other exposed parts of the PCB, including copper traces, from environmental pollutants including chemicals, dust, and moisture. This guarantees the long-term board durability by preventing copper oxidation and corrosion. Shielding the PCB from outside elements helps the solder mask preserve circuit electrical performance and stop early degradation.
2. Insulation
Particularly between closely spaced copper traces, one of the main functions of the solder mask is to offer electrical insulation between several conductive portions of the PCB. By making sure solder just sticks to designated, exposed places like pads and vias, this insulation eliminates inadvertent short circuits during the soldering process. Reducing the danger of electrical problems helps the board to be much more operational.
3. Aesthetics
Although sometimes disregarded, a solder mask's appearance is crucial especially in circuit identification and troubleshooting. There are several colours of soldering masks; green is the most often used one. Easier solder joint and component examination is made possible by the mask's visible contrast with the uncovered pads. This enhances control of manufacturing quality and enables personnel to spot problems during repairs or maintenance.
Examples of Effective Solder Mask Designs
Excellent solder mask designs are distinguished by their accuracy, alignment, and utility, therefore guaranteeing that the PCB runs consistently and satisfies design criteria. Here are some well-made solder mask samples together with their effective characteristics:
1. High-Density PCB with Fine-Pitch Components
High-density PCBs with fine-pitch components, including Ball Grid Array (BGA) packages, clearly show an efficient solder mask design. In these situations, the solder mask has to exactly mark the places where solder is deposited without invading adjacent pads. The design guarantees that the solder mask apertures exactly line the pads, therefore avoiding solder bridges between closely spaced connections. Here, Liquid Photo-Imageable (LPI) solder mask is rather popular since it provides the required high resolution for such complex patterns. The efficiency resides in the close control over alignment and clearance, so minimising flaws and raising yield.
2. PCBs in Harsh Environments
PCBs used in demanding settings, such automotive or aerospace uses, also exhibit another good example of solder mask design. Thicker solder masks on these boards help to offer better defence against moisture, chemicals, and thermal cycling. Apart from the solder pads, the solder mask covers all exposed copper regions to guarantee strong insulation and corrosion prevention. Key to their efficacy in these designs is the solder mask's endurance and environmental stresses' resilience.
3. Multilayer PCBs with Tented Vias
Tented vias are used in multilayer PCBs whereby the solder mask completely covers the via holes to stop solder wicking or contamination. Better electrical integrity and protection are guaranteed by this design. For complicated, multilayered boards, this method is quite successful thanks in great part to the solder mask's exact growth around the vias.
Conclusion
Crucially important in PCB design and manufacturing, solder masks offer durability, insulation, and necessary protection. They improve general dependability, shield copper traces from impurities, and stop solder bridges. Based on design requirements, several kinds of solder masks—including liquid photo-imageable (LPI) and epoxy-based ones—have various advantages. Applied techniques guarantee exact mask installation via screen printing and photo imaging among other things. PCB performance is improved even further by thoughtful design factors including thickness, coverage, and alignment. Including these elements produces PCBs that satisfy strict industrial standards and are more durable, efficient, and high-quality.
Table of Contents
What Is a Solder Mask and Why Is It Essential?
Key Design Guidelines for Solder Mask Design
Types of Solder Masks and Their Applications
Standard Thicknesses for Solder Mask Layers
IPC-SM-840 Standards for Solder Masks
The Application Process: How Solder Mask Is Applied
Understanding Peelable Solder Masks
Solder Resist vs. Paste Mask: Key Differences
How To Manage Solder Mask Defects: Common Issues and Solutions
Solder Mask Design Considerations and Best Practices
How to Incorporate Solder Mask into PCB Designs
Examples of Effective Solder Mask Designs
FAQ's
What is the purpose of a solder mask in PCB design?
In PCB design, a solder mask serves mostly to shield other exposed regions of the board from oxidation, contamination, and short circuits during the soldering process, therefore safeguarding the copper traces. It guarantees solder just sticks to the specified pads and vias, therefore insulating the non-soldered sections. Moreover, the solder mask shields the PCB from external elements like dust and moisture, therefore offering long-term endurance. Its importance is great in avoiding solder bridges and improving the general lifetime and dependability of the board.
How do different types of solder masks impact PCB performance?
Via their material characteristics and application techniques, different solder masks affect PCB performance. Though they provide basic protection, epoxy-based masks lack the accuracy required for intricate designs. Often employed on high-density boards, liquid photo-imageable (LPI) masks offer outstanding resolution and endurance, hence supporting fine-pitch components and multi-layered PCBs. Perfect control over thickness made possible by dry film masks guarantees strong protection for sophisticated designs. Especially in demanding conditions or high-frequency applications, selecting the correct solder mask type improves the protection, electrical insulation, and performance of a PCB.
What are common issues with solder masks, and how can they be fixed?
Common solder mask problems include air bubbles, slivers, inadequate covering, misalignment of registration. Usually solved by exact photomask alignment and enough clearance between pads, slivers can create short circuits. Changing application parameters for even distribution helps to solve incomplete coverage by leaving copper exposed. Inaccurate registration causes misalignment; thorough imaging process calibration can help to fix this. Correct application causes air bubbles; they can be avoided using vacuum techniques to release trapped air during cure.
How should solder masks be incorporated into PCB design files?
During the layout stage, solder masks should be meticulously included into PCB design files utilising tools enabling mask layer definition. Usually shown as a negative image, the solder mask layer lets exposed parts remain free for soldering. Correct mask alignment depends on designers specifying appropriate clearance around pads and vias. Gerber files and other final design files have copper, drill, and silkscreen layers along with solder mask layers. Effective production and dependable board performance depend on exact integration of solder mask requirements.