Over the years, components used within electronics have undergone a rapid change with one of these being the Quad Flat No-lead package (QFN). Its style is now integral to modern-day electronics both for its appearance and premium performance. QFN packaging is also great for space-constrained devices since it has a small form factor and no leads to stick out. Featuring a flat form factor with limited footprint, it is suitable for high performance applications lacking space like mobile devices and wearable technology.
The QFN package is awesome at power and thermal management plus compact almost bulletproof size. The reduction in signal delays and the improvement of the signals integrity is important in maintaining flawless operation of high-speed electronics. Since the package's underside is little more than a thermal pad, heat can escape quickly from even heavily worked components. Over the years, as electronics have continued to shrink, requiring more power and higher performance in small form factor designs, QFN has become the first choice for engineers looking to optimise functionality & compliance of modern compact boards.
Key Highlights
- The Quad Flat No-lead package is a surface-mount technology that provides necessary support in contemporary electronics.
- You can reduce excess inductance, improve thermal performance, miniaturisation, and cost-efficiency with QFN packages.
- The different types of QFN are plastic QFN, AC QFN, and type thin QFN.
- You must line QFN perfectly with PCB pads, heat the PCB for anchoring, ensure usage of solder stencils, and carefully control heating as well as cooling stages to make a reliable QFN.
- Even though QFPs have longer leads that make them easier to inspect and rework, they take up more space on the PCB as compared to QFN.
Understanding QFN: What Does It Stand For?
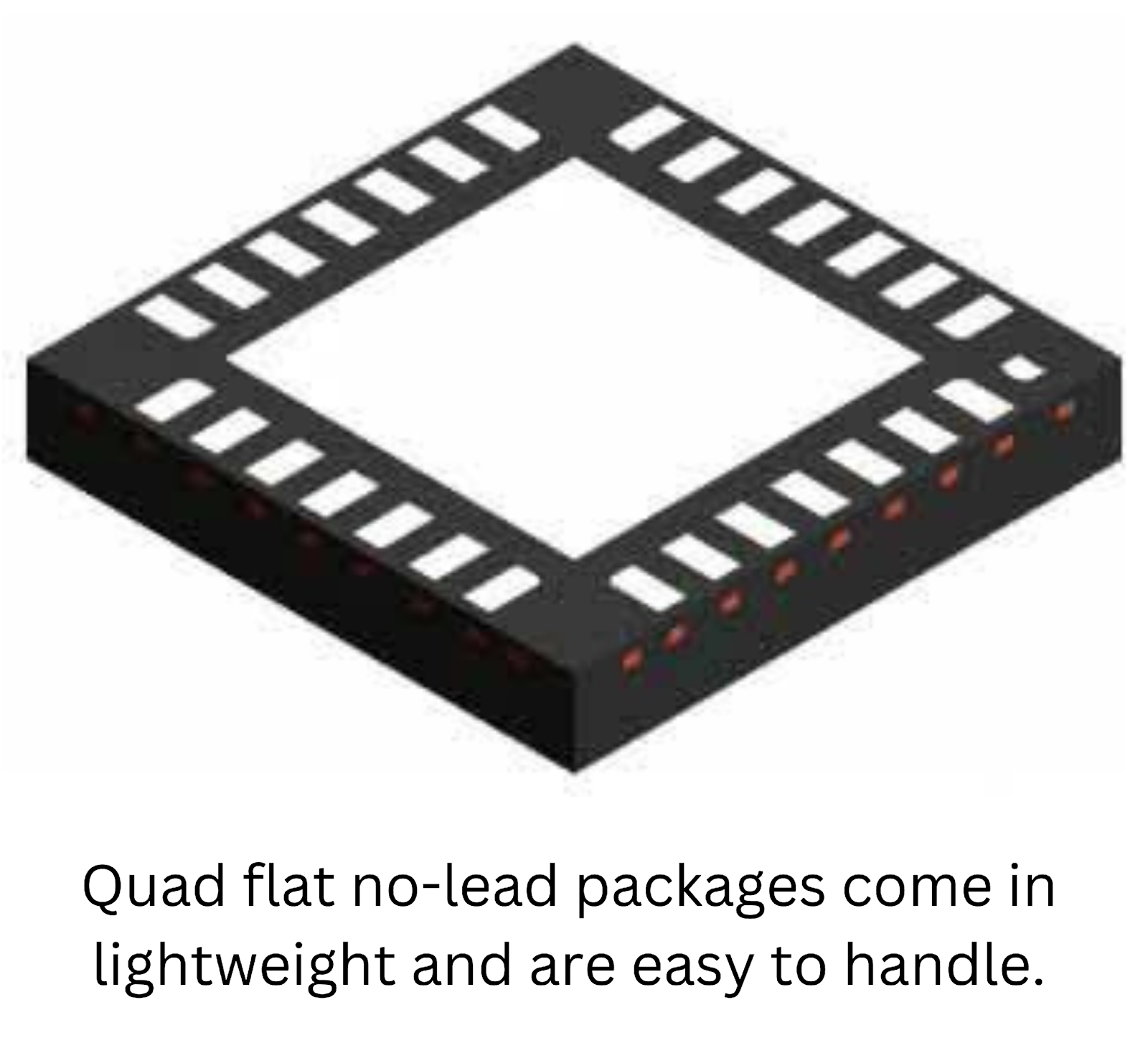
The Quad Flat No-lead package is a surface-mount technology that provides necessary support in contemporary electronics. QFN — short for Quad Flat No Leads, named after its four straight sides which have connections going out from them. The package ships flat, which of course is where that descriptor comes from. While most packaging types have pins sticking out that components can be mounted to, QFN stands for "no lead" as it has no exposed leads. The QFN packages have pads on the bottom and these are electrically connected to PCB components via direct contact.
QFN packages emerged as a response to this demand for better circuit performance while occupying less die area. Then, as engineers were working to make devices smaller and more powerful than ever before they sought new packaging solutions that would increase power output per unit volume weight of the fuel without adding mass. Because QFN packages can handle high-frequency signals, dissipate heat well and offer strong mechanical performance with the smallest end product size they have emerged as the top choice.
Inside the QFN Package: Exploring Its Components
QFN stands for Quad Flat No-lead which means that it is a package having small, durable and also efficient structure. At the centre of this is the die, which is just the name for a very flat, tiny piece of actual semiconductor containing all these goodies that actually do stuff--the things we call microprocessors—are built using bundles of similar components.Lead Frame copper holds the dice and provides support as well an electrical pathway. A die is attached to the lead frame by conductive glue or solder. It also guarantees a firm conductor link. Next, little gold or steel wires bond the die delta with each other and also to their own inward leads of the lead structure.
That is done through wire bonding. These inner leads become electrical lines that terminate in small flat pads on the bottom of the package. Those pads make contact with the printed circuit board (PCB) when mounted. It permits connection to an electrical system without the use of conventional leads that protrude from package sides.
Contrary to other packages of the time (like QFP = Quad Flat Package), which used visible pins or leads from one side and stands for all four sides, QFN had a different approach. QFN doesn't have any leads. The primary benefit of QFN packages is that they have no external leads, allowing them to be much smaller and providing improved electrical performance by reducing lead inductance or minimising the path from die-to-PCB flow.
In addition, encapsulation is used to protect the die and internal connections from external harm by sealing. This can be done by covering certain types of components in plastic or clay to insulate the inside parts and help maintain a slim package. Large mechanical and visible thermal pad on the bottom of the package further enhances QFN performance by removing heat generated in the die very quickly. This ensures that the device functions with high reliability even when under heavy load.
Key Benefits of Using QFN Packages in Electronics
In modern electronics, when one is looking for a small size and good performance QFN (Quad Flat No-lead) packages are perfect due to several reasons.
- Reduced excess inductance: Since the package has no external leads, this means a shorter path for electrical links between die and PCB. However, the parasitic inductance is drastically improved by reducing lead lengths. This increases signal integrity and hence QFN packages are ideal for high-speed,high-frequency applications where performance is crucial.
- Better thermal performance: QFN packages typically have an exposed thermal pad that is soldered directly to the PCB on its bottom side. This enables easy heat dissipation from the die to PCB, thus preventing chip getting hot and running smoothly even under heavy load. The power-efficient design is quite helpful for devices with high thermal efficiency, such as smartphones and wearable tech where size matters too much without performance loss.
- Miniaturisation: QFN packages are a thin wafer of silicon with tiny bits and bobs sticking out around the edges, they're great for small gadgets or anything you want to be portable. As they occupy less space, designers can include more of them within ever smaller footprints — a key trajectory in the quest to continuously miniaturise devices. QFN packages are tiny, but fast For this reason, they are ideal for many uses.
- Cheap: They are simpler and less expensive to manufacture than other types of packing because they have no sticking leads. Low production costs are one advantage of these simple constructions, frequently formed by reflow soldering (on a simpler configuration).
What Are the Different Types of QFN Packages?
Different uses have different temperature, electric and mechanical requirements so we can find QFN packages to suit the needs.
- Plastic QFN (PQFN): This is the most common type. The die is cased in plastic, albeit not as fancy as the G.Skill Trinity RGB light show: it will make the DDR4-4000 chip “more durable and comes with a longer lifespan. This is useful in cell phones, consumer goods, anything you need to make millions of. This is why they are covered with plastic, which makes the production of them cheaper and at the same time this material provides a good electrical performance and dissipates enough heat in daily use devices. Good people favour PQFN packages despite the fact that they could choke up under regular load. Which is why institutions that need to scale fast and furiously, love them.
- AC-QFN: It is manufactured for specific and high performance applications, such as RF (radio frequency) and microwave circuits. The AC-QFN is different from the fully-encased PQFN in that it has an air gap between the die and package. This will reduce the dielectric constant and signal transfer is proper. For high-frequency tasks, which need to maintain signal purity, it helps a lot. The air hole is designed to cool down the temperature more easily when a larger power needs to be dealt with by package.
- Type Thin QFN (TQFN): Designed for very thin packaging applications such as wearable tech and other small footprint devices. QFN packages are thinner as compared to regular PQFNs, so these are found suitable for low profile devices mostly. The thinner profile does not mean that they have any less in terms of electrical and thermal performance compared to the QFN. This means they are both small and powerful. All are used within an examined package type, the QFN family, to serve unique use cases including low-cost/high-volume production; enhanced thermal performance requirements for high-power devices or a compact signal chain and small very thin form factor.
Designing the Perfect QFN Footprint for Your PCB
- Ensuring you have the correct QFN footprint for your PCB is crucial to both design and assembly, as well as ensuring long-term reliability. The QFN package has its footprint on the base. This is the one that will decide how good it can be mounted onto your PCB, wherefrom to get rid of heat and make some decent solder joints. An incorrect footprint design can lead to failure during the PCB assembly process, bad heat performance or (in a worst-case scenario) the component ends up not functioning at all.
- Align the QFN pads with PCB pads. This involves much of the hand counting how big parts and spaces have to be, both for good soldering jobs as well as safety from damaging machinery. Each pad should be large enough to create a reliable solder joint but small enough so that the solder is not able to bridge between adjacent pads.
- Opening of the solder mask should be done in accordance with the manufacturer's instructions for reliable soldering. The mask has to fit exactly on the pads while still allowing enough spacing for solder paste. Thermal vias are a critical part of QFN footprint design, particularly when the package has an open thermal pad. These are vias that allow to transfer heat from the QFN package, then heat escapes more easily through them.
- There should be many vias placed just below the thermal pad, which can all connect to a large land on the PCB in order to control heat effectively. Here, the QFN package is set up in a manner that it cools down very quickly due to which there are less chances of its getting too hot. Similarly, fix a proper amount of solder paste to the thermal pad in order to obtain a good thermal and mechanical connection during the reflow process.
- Of course, the design of the stencil may prevent you from running into problems such as voiding or missing solder joints. To create a QFN footprint that is stable and conductive heat, adhere to these guidelines. This leads to strong performance and good cooling.
QFN Assembly: Best Practices for Success
QFN assembly requires placement and soldering to exactness as well, so you will have to mind all the small details due to its leadless design.
- The QFN package is to be placed on the PCB. As a rule this is done using pick-and-place tools of choice. Since QFNs have no protruding leads, they must be lined up perfectly with the PCB pads to make proper electrical connections and prevent misalignment problems that can result in a non-working circuit..
- Solder paste is smeared on the new pads and the PCB is heated up for solder melting to anchor the QFN package. Voiding under the thermal pad can also contribute to trapping heat within and degrade package performance, so a well-controlled reflow profile is also critical.
- To prevent voids, you will need to have the solder stencils made right and also consider vacuum reflow or nitrogen for your soldering process.
- By carefully controlling the heating and cooling stages to avoid problems such as tombstoning or missing solder bonds, optimising the reflow process guarantees that you will always get consistent results. By following good processes for precise placement, controlled soldering conditions and careful management of the reflow process you can make a reliable QFN assembly.
How Are QFN Packages Soldered on a PCB?
The reflow soldering is the best way to create strong connections with proper component position when surface mounting QFN packages on PCB. This process actually begins with placing a stencil for solder paste to be positioned on the pads of PCB. The stencil shape was extremely important to get the correct amount of solder placed, especially on the thermal pad under QFN package structure.
Well-aligned stencil holes control the volume of solder that flows, and prevents issues like short from neighbouring pads (solder bridges). The QFN package is placed onto the PCB via a pick-and-place machine which automatically aligns it, after solder paste has been applied.
The PCB would then be inserted into a reflow oven and the heat within the process melts the solder keeping your expensive parts secured. This creates solid connections between the QFN and the board. Solder bridging and Tombstoning are both frequent issues that occur during this process.
The former is solder bridging, when an excess amount of solder makes electrical contact between two pads; the latter is tombstoning: uneven heating causes a part to rise on one side. However, you can alleviate such issues by ensuring no stencilling design flaws are there, applying an appropriate layer of solder paste and fixing the reflow profile. Using these guidelines you will ensure that the QFN soldering process works fine and is reliable.
What is the Difference Between QFN and QFP?
QFN and QFP are both surface mount packages, but their structure, lead arrangement design meaning they as a component were wholly opposed in terms of how to use them. Check out their striking differences:
- Power supply is attached instead through flat pads on the bottom of the package, soldered directly to PCB. This form factor makes the QFN smaller and allows this design not to have any leads, reducing its size with it being perfect for high-density offerings that need space savings such as high-frequency circuits or wearable tech mobile devices.
- The QFP (Quad Flat Pack) package, which is a flat pack with leads protruding from all four sides at right angles to the plane of the base and offset in both directions along two mutually perpendicular axes passing through that point on each side adjacent to and farthest away from base but not overlapping onto or affixed parallel wise thereto. The circuit board has pads where these leads connect with copper traces to the other parts of the PCB; this is what makes its mechanical holder.
- Even though QFPs have longer leads that make them easier to inspect and rework, they take up more space on the PCB and can associate higher parasitic inductance which typically slows things down at high speed situations. As QFN don't have any external leads, thus they suffer from very less parasitic inductance which helps a lot in enhancing signal integrity. That makes them more suited to high-frequency and hammier-duty jobs.
- Moreover, QFNs are more competent in handling heat due to the thermal pad, which is evident and that directly outputs the performance requirement protocols. As a consequence, QFNs are superior for smaller footprints and the best electrical performances as well to dissipate heat.
Design and Structure of QFN Package
QFN (Quad Flat No-lead) packages are specifically designed for the optimal combination of thermal and electrical performance in a small package. The die, which sits in the middle of this package, is a semiconductor chip that performs device work. Conductive glue or solder is then used to connect the die with a lead frame made out of copper.
Naturally, this has to guarantee both strong mechanical and good electricity connection. The lead frame connects the die to the pads by wire bonding. The die gets connected to a printed circuit board through pads. The leads are not protruding from the outside but are flat contacts at the bottom side of the package. Because of this, it helps to lower parasitic inductance and raises the signal integrity especially at high frequency PCB applications.
The thermal pad ground exposure beneath the die is one of most critical parts in QFN packages. This pad allows for better heat transmission from the die to the PCB. And that makes the QFN packages great for heat dissipation. Copper is a good heat conductor and it's common that the thermal pad and lead frame are made of this material.
It is encapsulated in a plastic or ceramic shell, kept out of the rest of the world by wire bonds but also low profile. And this design which offers lower power, good electrical performance and small form factor makes QFN packages ideal for high Performance devices to be placed at a smaller place of placement say smartphones/RF peripherals/wearable tech.
Common Challenges in QFN Packaging
Generally, these are the issues you may encounter when you work on soldering and heat management (to name just a few) while using a small size of packaging.
- There are no leads on the outside and thus it's nearly impossible to get all contacts soldered correctly.
- Mistakes in alignment can cause electrical links not to work properly. Well, those flat pads are on the bottom of it and improved inspectability can't hurt (at least if you're looking for other issues that might have been inadvertently installed).
- Heat is another issue, particularly in high-power applications. This can result from incomplete thermal vias, or inadequate solder underneath the pad that causes air gaps and results in poor heat transfer.
In order to counteract these issues, great care needs to be taken in the design of a footprint so that solder mask holes and PCB stencil designs are optimal for consistent paste deposition. X-ray inspection is the only place to find secret problems, but vacuum reflow or a nitrogen atmosphere may reduce voiding in solder joints. This point is important as we need to check and test the QFN package on a regular basis such as functional, thermal cycle tests so that it should work properly when used in practical implementation. These methods allow manufacturers to mitigate the drawbacks of QFN packaging, allowing their devices to function properly and endure for longer periods.
Applications of QFN Packages Across Industries
QFN packages are widely used by many different businesses because they can operate on heat, provide good electrical properties and size too. The restriction to consumer electronics comes from the fact that they can cram such high-density designs into a limited space (e.g., phones, tablets and wearable tech); where you have just enough room but not too much for keeping heat under control.
- Automotive: QFN packages are widely used in the automotive industry for, e.g., power management IC and control unit due to its ability to work well under critical conditions allowing heat dissipation. They are thus ideally suited for advanced driver assistance systems (ADAS) and the power electronics of electric vehicles, since these work reliably even when subjected to high loads.
- Industrial: QFN design works excellent for motor control units, sensor modules and similar space-saving needs in industrial automation.
- Technology: The low parasitic inductance and excellent signal integrity of QFN packages is great for high frequency RF circuits used, like telecommunications or wireless networking. QFN packages are poised to become more critical as technology continues to improve in performance for new applications like 5G infrastructure, medical devices and Internet of Things (IoT) markets. While these are likely to be smaller, less power-hungry and probably faster areas.
Conclusion
In a nutshell, QFN packages have a lot to offer — they are tiny in size, excellent thermal managers and perform better electrically. They are used for multiple purposes, due to the fact that they can perform many tasks from high-frequency circuits to consumer technology and automotive systems. With the constant improvement of technology, QFN packages are only going to be more important for enabling smaller and more efficient devices. QFN can be an excellent choice for small packages and high-performance applications lightweight; it is a good option to consider at your next PCB design job.