In this video, Anoop B Sridhar (Product Manager, Fintech Space) and Murali Srinivasa (Founder, LionCircuits) are going to drive you from prototype to production. They talk about 4 main vectors to be considered at each stage while going from prototype to production.
Question: We have seen AWS bringing a change in the software space in going from prototype to production. How does Hardware space look like in terms of production?
Answer: There are some similarities. But however, Hardware manufacturing has a different set of vectors that we focus on. In production, to name some of the vectors and that would be Production Management, Quality, Factory capacity, and Supply chain management. So, these 4 vectors change as you go from one stage to another depending on the batch size that you are working on. The batch size can be different, but it is easy for us to compare different vectors if we consider something like 10 to 100, 100 to 1000, 1000 to 10000, and beyond.
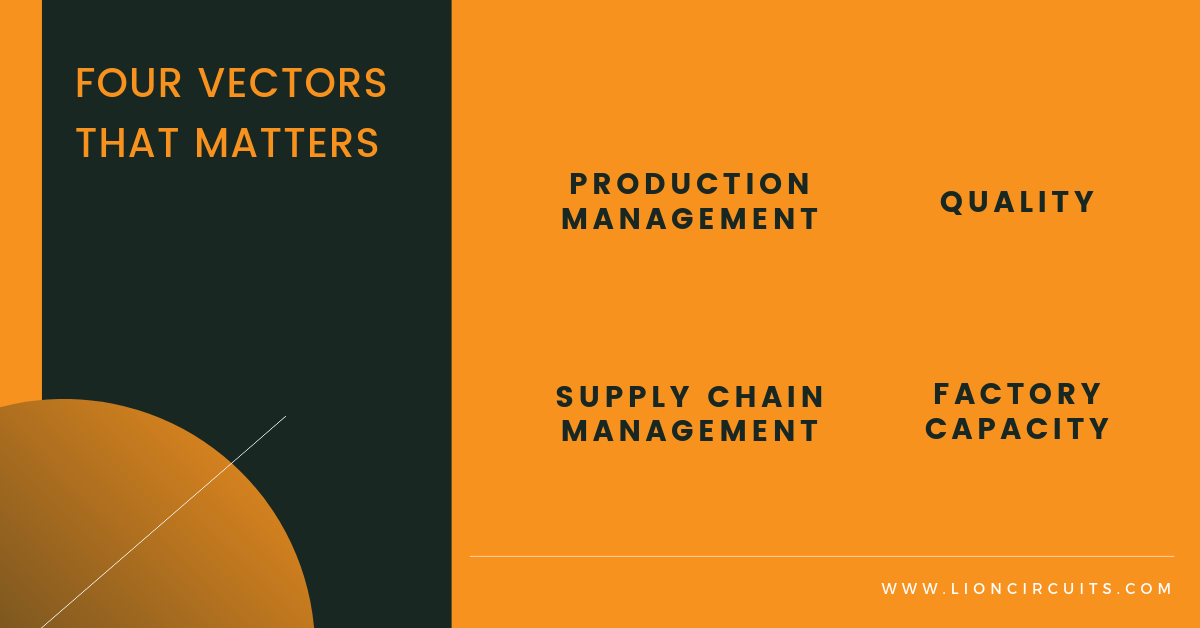
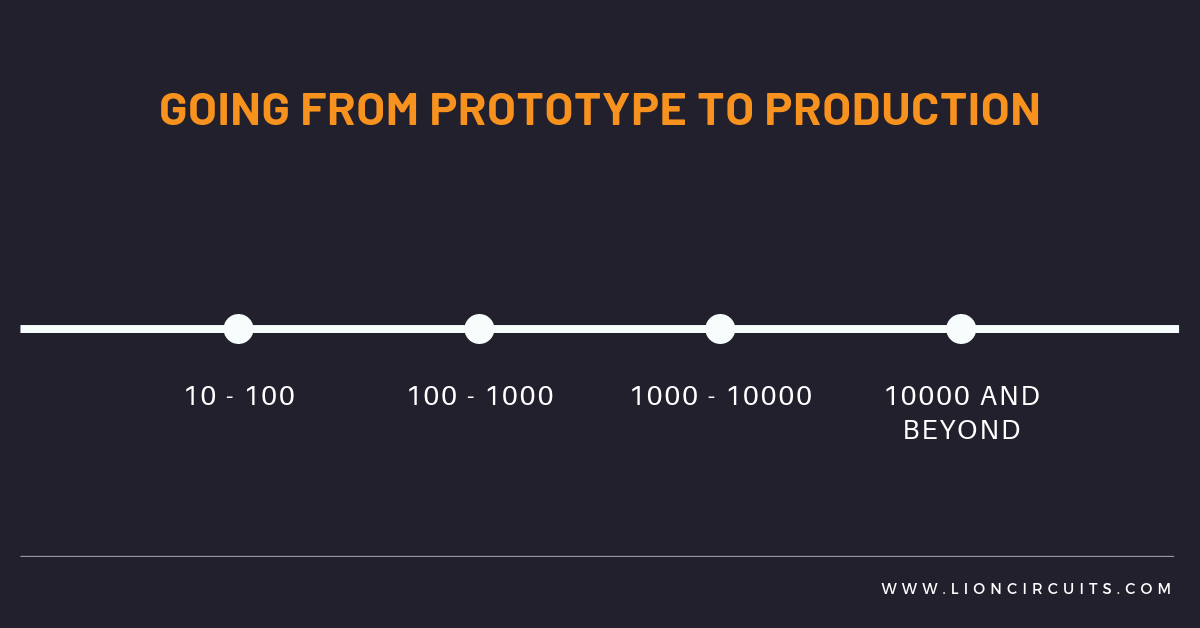
Question: Let’s then start off with the lowest unit which is 10 to 100. What matters when somebody wants to come up with their first 100 units in production?
Answer: When you are working on ramping up from 10 to 100 units, you will be typically focusing more on product-market fit, making sure that the product has a place in the market, so you will be mostly tweaking your designs making sure that your customers are happy. However, you will also start to think about functional testing in production, component sourcing, and all the other vectors that we discussed. You will not get into it too much, but, you know things start to take importance at this stage.
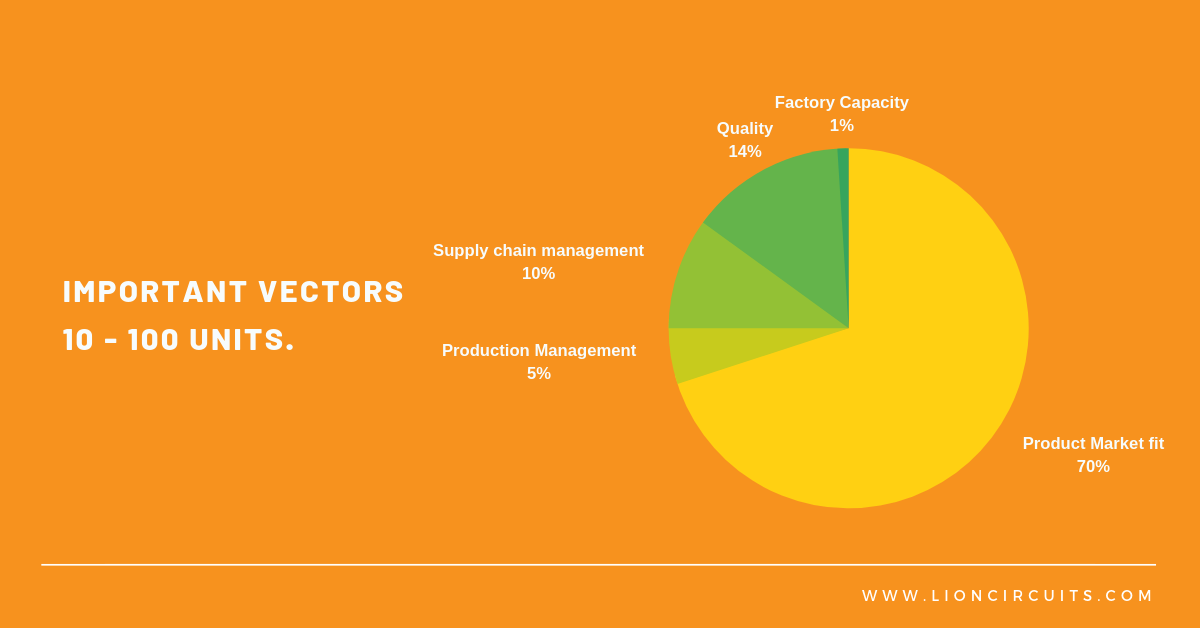
Question: So, Product-market-fit, like folks in software do some user testing, that’s the kind of stage we are still in. I believe the next step is where things start getting heated up and so, how does it look from 100 to 1000 units.
Answer: I think this is a very interesting phase because you know as a start-up you would be giving from 100 to 1000, So everyone is excited about it. Also, there are challenges that come along with production. So, the main 2 vectors out of 4 vectors that we discussed before that come into light in this segment are Supply Chain Management and Quality. You’d be working on test coverage making sure that your functional testing does a good job in terms of finding defects in the production and also you will start to think about supply-chain, making sure you have reliable vendors who can supply reliable components with as less component failure as possible. So, this starts kicking in at this phase.
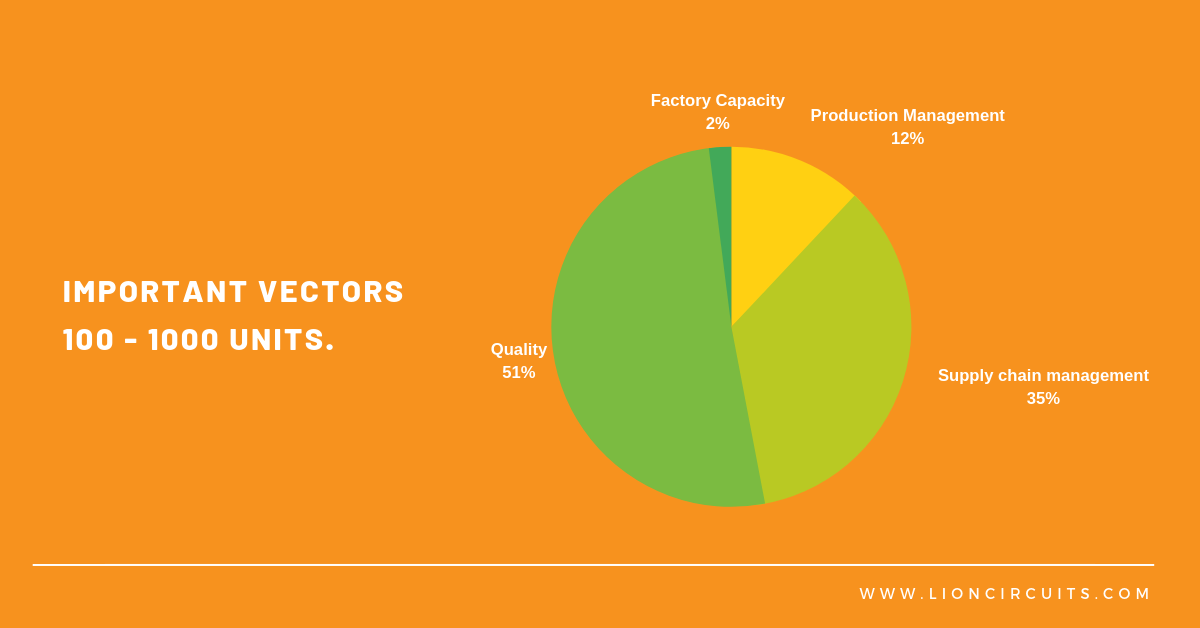
Question: Okay! I think the tools that you have built may be to get reliable vendors on board…
Answer: Exactly. I mean this is the phase, when the customers who are on our platform, who have developed 100, 200, 300 units, they would be sourcing components of their own. But beyond 100 when you are going from 100 to 1000 is where we can help you in Component Sourcing as well. With the tools that we have developed in house, which will do certain things in terms of helping customers, define the right vendor, cost, comparing different components and certain things which you would not get outside. These are some of the value additions you would get from LIONCIRCUITS.
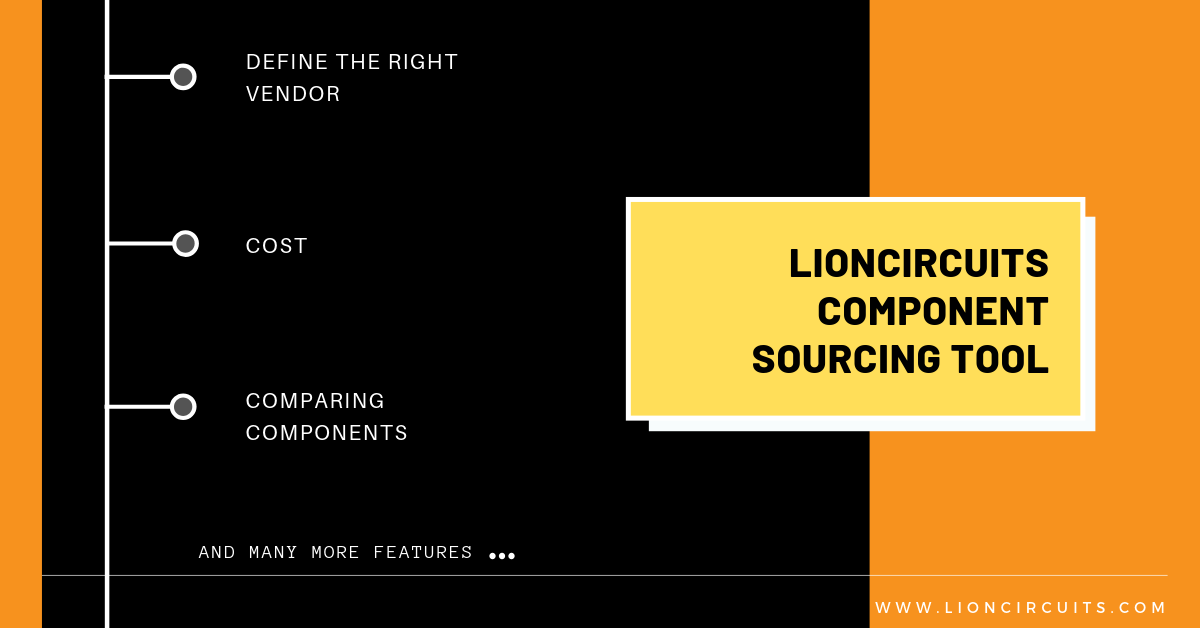
Question: Well, that’s interesting and we are now covering and the game is heating up. Now, How does it change from 1K units to 10K units.
Answer: So, then you know it’s more exciting as a start-up when you are working hard and you see your product now flourish in the market, you are gonna now accelerate from 1K to 10K. However, the challenges also increase in terms of manufacturing but, hey…! you are covered with LionCircuits. A dedicated manager would help the customer navigate from 1K to 10K. Key things that a start-up would face or a company would face in terms of going from 1K to10K would be again component sourcing in terms of lead times. There will be major lead times, factory lead times with the components, which the customer has to work with factories directly to make sure that we forecast the order production so that we get components on time, that’s the critical piece of it. And the second most important factor is quality. In terms of quality, making sure that you have a good yield, focusing on yield and improving the yield and using different tools which can help in quality improvement, would be a big factor here.
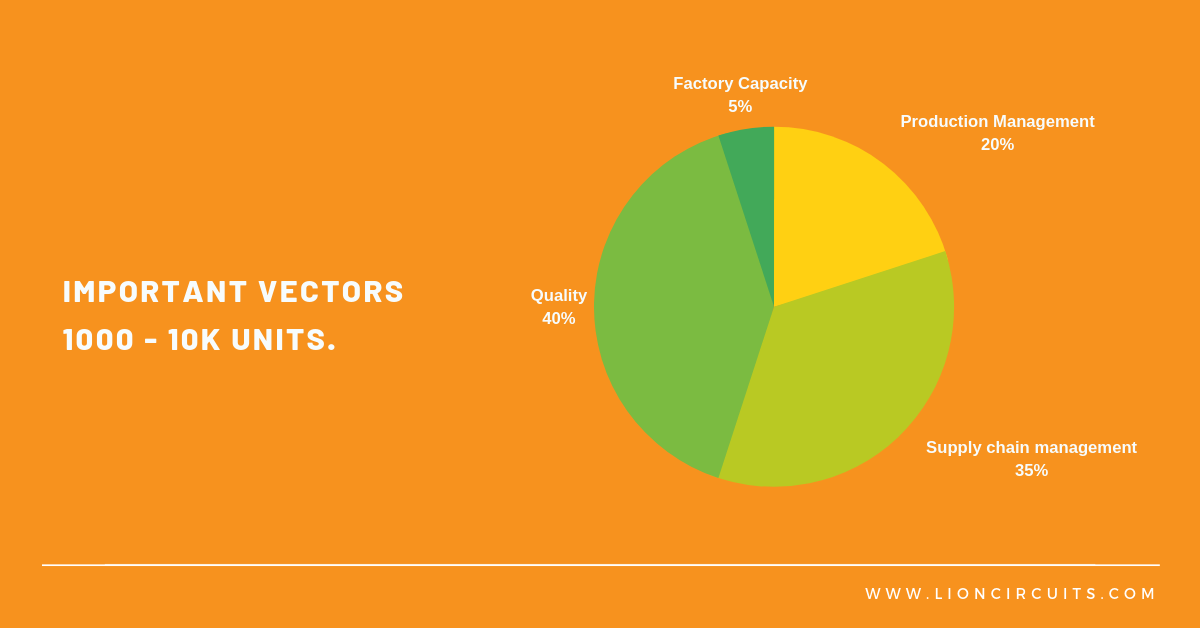
Question: So, What are the things to take care of here and what tools you provide?
Answer: The Bill of Material Optimization (BOM cost optimization) is a very important thing because every single Dollar at 10K starts to matter, right. So, that is where optimizing Bill of Material for cost becomes important. We have internal tools related to Bill of material optimization that we have developed which we use to help customers; optimize their Bill of materials. And, in terms of quality, we also have another division in LionCircuits, which is Tooling AI. Where we develop AI-based quality inspection tools. We train a model for a specific production (application), that is happening in our production line to control certain quality-related defects, maybe something like visual inspection tuned to a particular application. So, these are the things that we can do with the current technology. And, these are some of the things that we are currently using in LionCircuits for production.
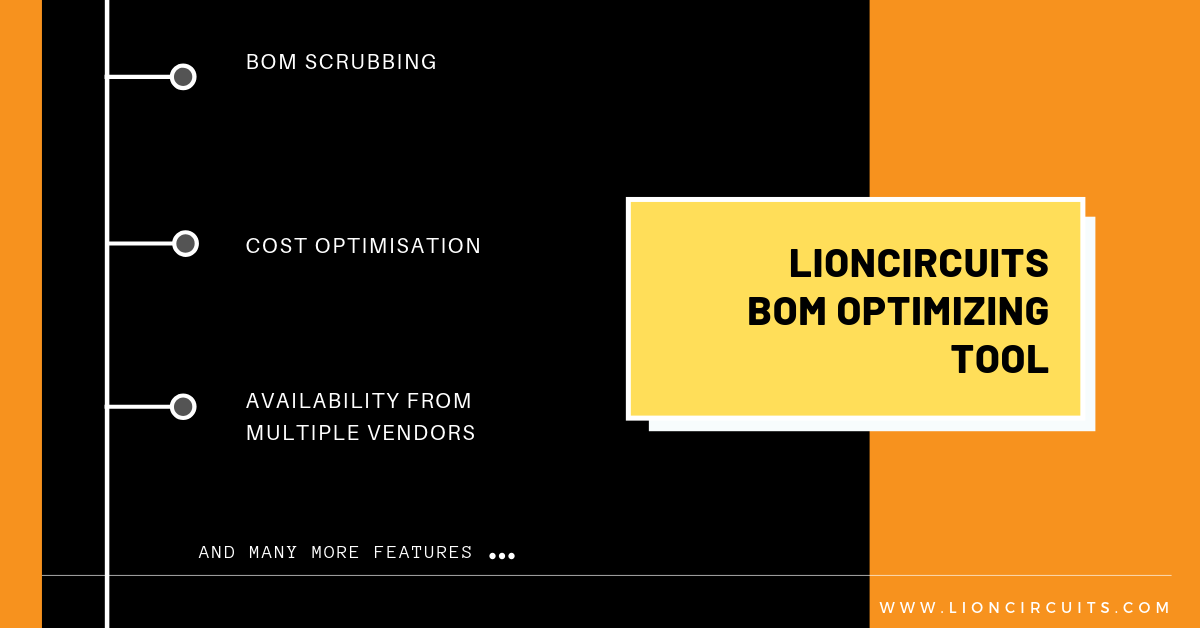
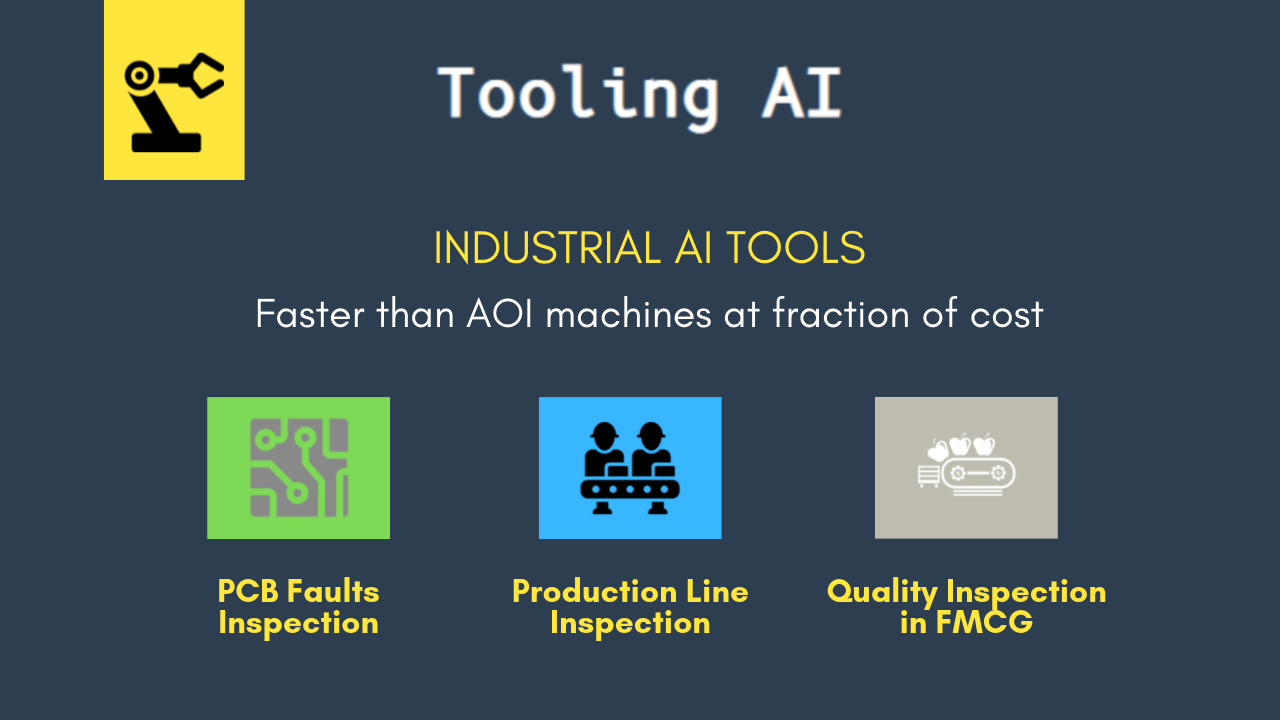
Question: So I am guessing this covers most of it. What is there when you go 100K and beyond?
Answer: I think it’s the 4th vector, that we have not yet discussed , which is Factory capacity. Typically, people will go from India to China or from anywhere in the world would go to China and get it manufactured there, outsource manufacturing there to contract manufacturers. However, in recent times, we have seen that the labor cost in China has increased significantly when compared to that in India. And, also not just that, in terms of the economic and political scenario, India is a really good country to set up manufacturing plants. When you really look at a 100 K units or close to it, what happens is the unit economics would really make sense for manufacturing units in India when compared to manufacturing in China and then paying for duties and lot of other additional costs that are involved in getting the products from China to India. So, that offsets and it becomes more lucrative to the manufacturer in India. I think that’s where, you know we are in talks with few customers to set up such dedicated facilities, and it is looking really positive.
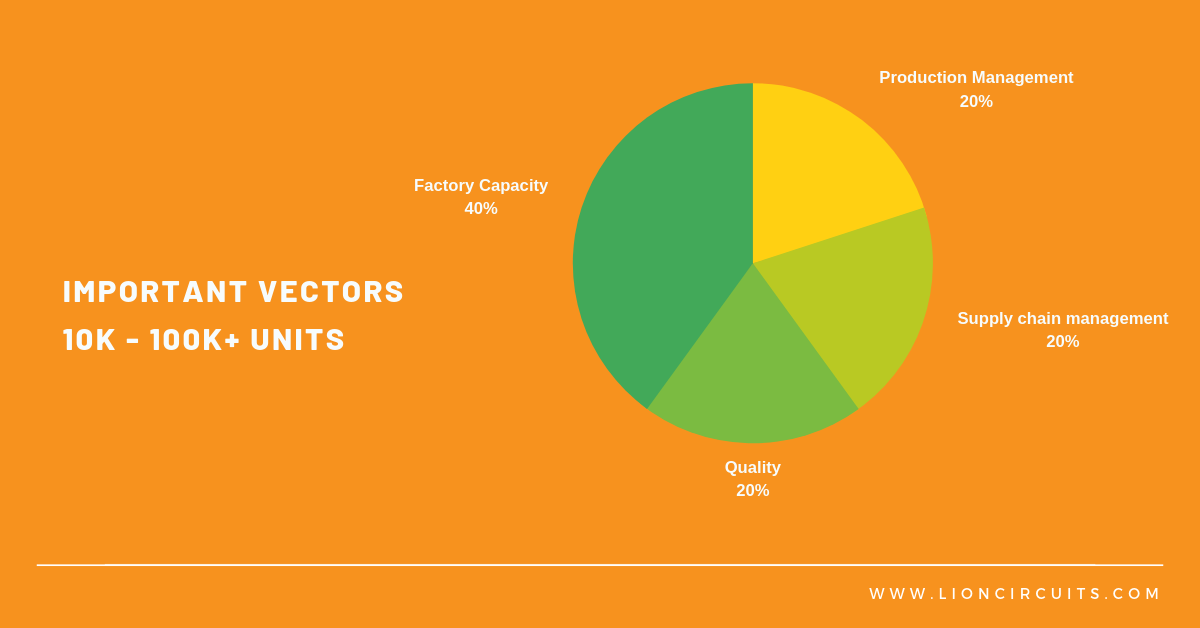
Great, that’s interesting. Maybe the next step is in terms of taking out China, And, its a flavor of the season, where we are close to independence day. Maybe freedom from manufacturing in China.
Definitely, I think that’s definitely gonna happen and we are really positive about it. The way things are going currently, a lot of big mobile phone manufacturers are working with the Chinese contract manufacturers to set up operations in India, which means that there are a lot of opportunities here which we should recognize and, you know, start giving serious thought about it to manufacturing in India.
Right! Let’s see how this takes off. All the best for the endeavors in going from prototype to production.
