Gerber files are the preferred form of PCB design and also an essential element in manufacturing. These files specify all the fine layers present on a PCB such as copper traces, silk screen, solder mask and drill holes which dictates how manufacturers should fabricate true-blue circuit boards in the desired quantity. Originally developed by Gerber Systems Corp, it has become a common format for PCB designs because of its accuracy and versatility.
Gerber files make communication between designers and manufacturers seamless, reducing the risk of errors due to misinterpretation. They affect PCB manufacturing in a big way because they give us standard ways to specify the layout of each layer and thus improve efficiency during production. Moreover, Gerber files are also easier for prototyping makers as they can quickly introduce any changes to the design if needed. Standardising PCB data across multiple platforms All of these things go towards standardising the way that print-ready files can be sent to one-stop manufacturing shops, making rapid electronics prototyping almost child's play.
Key Highlights
- Gerber files are open ASCII vector format files that serve as the standard for PCB manufacturing processes.
- In the case of a single-layer PCB, these Gerber files will be simpler but multi-layer PCBs need extra Gerber files to handle its complexity.
- Layer data in Gerber files shows layers of the PCB while drill data offer specific instructions for making holes into PCB.
- Gerber files typically have a .gbr extension, though some variations exist depending on the software and version used.
- You must import the gerber files, inspect each layer, check design parameters, and run DRC to interpret Gerber data.
What is Gerber Files ?
Gerber files are open ASCII vector format files that serve as the standard for PCB manufacturing processes. Though definitely not the core of printed circuit board (PCB) design Gerber files do indeed play a rolled corner in it by being the most useful file format used for transferring data from designers to manufacturers. In this file are the PCB´s plans, based on them it means that each layer of the circuit can be an accurate PCB fabrication process and is called Gerber for its creator company "Gerber Systems Corporation".
Simply put, Gerber files primarily provide the manufacturer with information related to Copper layers, Solder mask Layers, Silkscreen Layers Drill Information. Generally speaking, the file format complies with RS-274X standards; this makes it possible to describe shapes or layers in much detail so that when a PCB is fabricated/built, no deviation from design specification should occur. Multi-layer PCBs are produced through a sandwich process, with each of the layers ideally represented by an individual Gerber file.
The key components within Gerber files include:
Copper Layers: Files for the electrical pathways on which all components will be connected. They provide accurate trace routing and signal integrity across different layers of the board.
Solder Mask Layers: This set of files contains the items that need a solder resist to prevent copper traces from being exposed and avoid corrosion leading to short circuits, enhancing long-term durability.
Silkscreen Layers: Silkscreen files are used to label the PCB, with component IDs and visual information(outputs a human-readable layer) The layer shows how the components of the board are put together and what they look like.
Drill Files : The Drill files specify the location and size of holes which are required to mount components or connect layers. These files guarantee that vias, through-holes and component leads are effectively positioned while manufactured.
These are an important part of the production process, as they contain essential details on how a board will be laid out, which in turn helps manufacturers understand exactly how to produce the designed PCB. In addition to designer information, the Gerber files provide a valuable component of streamlined manufacturing as it represents an industry-standard format that is universally recognized in electronics.
The History and Evolution of Gerber Files
Gerber files have a history that can be traced back to the 1960s when Gerber Systems Corporation invented it to assist in the standardisation of data communication during PCB manufacturing. The Gerber file at that time was known as the RS-274D format, a rudimentary vector plotting system that only conveyed basic points like coordinates and aperture information.
It was not until the 1980s when the RS-274X came to the scene, radically changing the Gerber system by embedding apertures, attributes, and layer-specific commands. Other than reducing the rate of data entry errors, the new format also facilitated the effective creation of complex PCBs and facilitated their accurate transmission across different platforms.
The growth of Gerber files has been directly proportional to how fast they could adapt to technological advancements. The shrinking sizes of solders and their complexity saw the introduction of HDIs as a Gerber file variant. It is also essential to know that Ucamco manages all Gerber files today and has continued to be used in modern designs such as 3D printing and AOIs.
Generally, the growth of Gerber from RS-274D to RS-274X is a clear indicator of how manufacturing is heavily reliant on technology to convert digital designs into tangible units.
Gerber Files as ASCII Text Files
In its simplest form, a Gerber file is an ASCII text that contains information about any layer of the physical PCB. Everything on a PCB, like copper traces or drill holes and silkscreen patterns, is encoded using plain text characters. Detailed, layer-specific instructions that can be readily understood by machines in PCB manufacturing are congenial to ASCII representation.
A Gerber file is a flat text formatted such that all the commands, coordinates and parameters are executed in sequence. These are orders for meaningful geometric shapes, line widths, layer settings and other design items needed to fabricate the PCB. The ASCII format of Gerber files allows them to be used across different systems, irrespective of design equipment or manufacturing machinery being employed — no need for a bespoke system.
Benefits: Being able to use ASCII text is a major advantage for the readability of Gerber files. Designers, engineers, and manufacturers can open these files in any text editor to check their contents, and they can even manipulate them manually if necessary. By the very nature of this kind of flexibility, Gerber files are universally compatible with a number of platforms and tools, allowing them to be utilised across an assortment. Moreover, ASCII text is lightweight, hence, more efficient to process and consumes less storage.
Limitations: But the simplicity of its format as ASCII-file also comes with some restrictions. It is significantly less efficient than binary formats in terms of data compression and speed. When working on large, complex PCB designs this method can generate long files that take longer to interpret and thus require more processing power. In addition to being human-readable, Gerber files can be challenging for those who are not well-versed in the command structure and syntax.
While using ASCII text in Gerber files is generally convenient and universally compatible, it may require more processing power on bulkier drawings.
The Role of Gerber Files in PCB Manufacturing
Gerber files play a crucial role in PCB manufacturing, serving as the digital instruction set for all other parts of printed circuit board fabrication. Using the accompanying Gerber files, a manufacturer can efficiently and accurately convert from a resource that represents what is in a designer's head into an actual PCB. The files contain information regarding all the layers and components needed in order to manufacture each one accurately and precisely.
Gerber files that are Required for Production of PCB:
The fabrication of a PCB is going to be dependent on certain critical Gerber files, each serving an explicit part of the manufacturing process. The least amount of files manufacturers need are the copper layers, solder mask layers, silkscreen layers and the drill holes. In addition to the files that are required by PCB manufacturers, they may need a few other things such as assembly drawings and outline layers – especially for complex designs. Therefore, these are the files that enable every aspect of PCB to be correctly regarded and implemented.
Copper( top and bottom ) layers: These files define the conductive paths on PCB, it includes every trace, pad and via. Only one copper layer file is needed for single-sided PCB. Multi-layer PCBs: Each copper layer will require its own file.
Solder Mask Layers: These are the solder mask files that depict areas on the PCB where a solder resist to be applied, thus protecting copper traces against corrosion and short circuits. These documents are expected for both single-layer and multi-sort PCB evacuation.
Silkscreen Layers: These files provide the board labelling which includes component indicators, pin 1 markers and branding. This is important for manufacturing and troubleshooting because this will allow manufacturers/assemblers to quickly identify the parts being placed.
Drill Files: The drill files define the positions and sizes of all holes on the PCB, be it for Vias, Through-Hole Components (THC) or mounting holes. It guarantees accuracy for drilling, which is especially crucial with multi-layer boards where holes have to line up across many layers.
Board outline: This file determines the dimensions and form factor of the PCB, ensuring that it will physically fit into an enclosure or system.
Single-layer vs. Multi-Layer PCBs
In the case of a single-layer PCB, these Gerber files will be simpler than those that only require one copper layer (the traces), solder mask top and bottom, and silkscreen. This is because part of the manufacturing process is dropped out, and as a consequence, it also becomes faster.
On the other hand, multi-fold PCBs need extra Gerber files to handle its complexity in design. It needs to be segregated into each copper layer with due solder masks and drill data for every layer. Nearly all multilayer PCB designs will have a power or ground plane layer, which must also be defined in the Gerber files.
The Role of Each Gerber File in Manufacturing
When this is done in the manufacturing of PCBs, one finds that every Gerber file actually has an important role to play. The Copper Layer files etch the conductive traces onto a copper-clad laminate. Solder mask files instruct where the protective solder mask layer will be applied to cover up any copper traces. The silkscreen files tell the printers where to add text and symbols, while the drill files direct drilling machines on how they should make all the necessary holes. The board outline file is needed to cut the PCB to its final size.
All of these files are important in making a digital design become reality and to do that the part is printed as close to CAD geometry as possible.
How Gerber Files Guide the Manufacturing Process
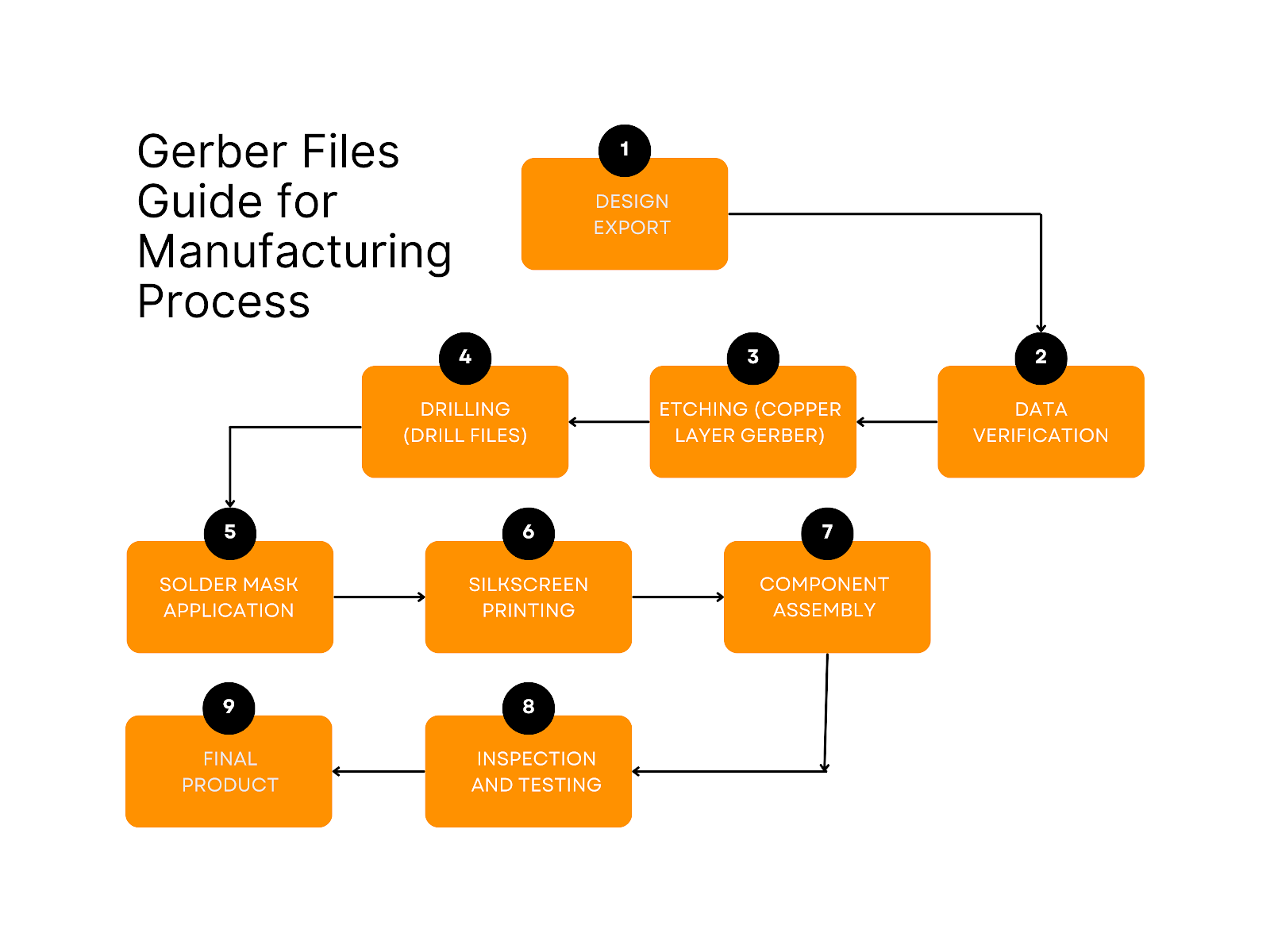
Gerber files are the centre of creating a PCB and tell manufacturers how to create boards in every stage of production. They make sure each layer of the PCB is properly fabricated, ensuring that what appears reflects directly with all design specifications.
Role of Gerber Files in Different Stages of PCB Production
- Design and Data Preparation: This process starts with PCB designers exporting the Gerber files from their design software. These files represent different layers of the PCB, like copper traces, solder mask and silkscreen. These files are quality checked and proofread to match the design intent.
- PCB Fabrication:
- Etching the Copper Layers: The copper layers are guided by the Gerber files, which guide the etching process. These boards are coated with a photo-resist, and the desired copper is exposed to UV light to etch out other areas (copper) and make conductor traces based on design.
- Drilling: Drill files contain coordinates and sizes for vias, as well component holes. This data is made use of by CNC equipment and plainly all openings are pierced via the board precisely.
- Solder Mask Application: The solder mask Gerber files tell the fabricator where to apply a material that protects circuit traces so the compound doesn't flow everywhere in tinned and unexposed areas of copper.
- Silkscreen Printing: This file will show where the component identifiers, markings and logos should be placed so they are in readable condition.
- Assembly and Inspection: Once the PCB is manufactured, Gerber files are used to verify that components have been placed correctly in accordance with design specifications. In automated inspection machines, the Gerber files are used to compare the physical board against the design for mistakes like unaligned traces or absent PCB components.
Integration of Gerber Files with Other Manufacturing Data
The Gerber files are combined with other accompanying data, e.g. the Bill of Materials (BOM) and pick-and-place files to aid in assembly of components on average PCBs. This embedding allows for continuous, consistent communication between various production steps potentially decreasing eventual misalignment and PCB assembly errors.
Principal Issues with Quality Control and Accuracy
Quality control of a manufactured board is extremely dependent on the Gerber files. They also provide exact details as to the construction of each layer and every singular hole, which allows manufacturers to adhere to tight tolerances in order that end products emerge without any defect. Automated inspection tools, such as Automated Optical Inspection (AOI) and Electrical Test (ET) machines, use Gerber files to compare the manufactured PCB against its intended design. This comparison makes it easier to catch faults before they hit the production line, saving time and money from expensive reworking and ensuring high board quality.
Data and Structure in Gerber Files
Gerber files are the most valuable data of PCB boards for manufacturing. These data are organised to give detailed instructions for all layers and components of the PCB. RS-274X is the default standard used to represent Gerber files that consolidate all required data into one type of file format, with unusual rarity in machen und Design modifications.
Types of Data in Gerber Files
- Layer Data: The data shows layers of the PCB, so copper layers are seen as a sequence, but it is also possible to see solder masks and silkscreens. Multi-layer boards will have more than two layers of copper, which this signal traverses. The Gerber files for each layer define where the conductive traces, pads, and other electrical features are to be placed. Solder mask layer data describes which areas must be insulated to avoid short circuits or copper traces from being exposed to the environment. Silkscreen has component identifiers, reference indicators, etc, which do not contribute to soldering the components but assist during assembly by enabling placement and identification of parts.
- Drill Data: The Drill data, or even the Excellon files, are richer in content and offer specific instructions for making holes into PCB. These holes are used for placing through-hole components, vias or mounting the PCB to its enclosure. The Drill files articulate where and how large each hole is so that the drills can know exactly its position to bore a hole. This data is essential for multi-layer boards as it identifies the VIAs that connect different layers and provide proper electrical connections across the board. They prevent the drill data from going off alignment which could otherwise affect connection failure or assembling issues.
How Data is Used to Create PCB Boards
Production machines refer to each Gerber file as they are used to generate a part of the PCB. For example, copper layer information instructs machines where to remove unwanted copper (and keep the area as empty extra space), whilst leaving certain portions behind for circuit pathways. CNC machines make use of the drill data to create holes for vias and components with extreme precision, while solder masks and silkscreens instruct protective elements (coating or labels) application. This clear separation of data helps guarantee perfect execution in all stages involved even down to manufacturing.
Understanding Data Representation
For a PCB to match the design specification, the correct data representation in Gerber files is needed. Data that is not error-free during transfer (faulty layer alignment, incorrect drill hole positions, or trace widths) results in faulty boards and is very expensive to rework if necessary. Failure of the entire project included! As a result, the precision of Gerber files ensures that all aspects of PCB fabrication are manufactured to exact tolerances and standards, leading to high-value reliable boards.
Understanding the Structure of Gerber Files
The structure of Gerber files is such that they provide all the necessary information about every layer going into a PCB. The RS-274X standard, which includes both image and embedded aperture information, is the most common. This means that the file can contain all information in terms of commands and coordinates required to correctly describe how parts are mounted on a PCB.
Gerber File Structure Overview
Every Gerber file contains a set of commands represented as ASCII text. These commands describe where everything is on the print: traces, pads and other features. The header of the file identifies in which units it is measured (inch or millimetres) and other information about the type of file. This file is followed by blocks of data that define the particles in terms of layer features, apertures and coordinates.
Breakdown of Sections and Commands
- Header: The header defines important details like the version of the Gerber format, units used for coordinates as well as type file. This provides a form of file type declaration and indicates how the digital data (file) that follows is constituted.
- Aperture Definitions: These set the shapes and sizes of drawing tools (apertures) used for creating traces, pads and other features. An aperture can be a circle, rectangle or other geometric shape.
- Coordinate Commands: The X and Y coordinate commands give the location on PCB for drawing lines, arcs or placing PCB pads. These commands are very important in drawing the complete layer of PCB.
- End-of-File Command: The file commonly finishes with a comply with eof, which merely tells the document is thoroughly sent and also protects properly closure format details.
How Structure Affects Manufacturing
Gerber files have a rigid structure that guarantees every step of the PCB manufacturing process is perfectly carried out. The header establishes the groundwork for how data will be processed. The aperture definitions and coordinate commands guide machines in PCB etching, drilling, and applying materials to the board. A clean, accurate and repeatable file reduces errors in the eyes of manufacturers who are left to machine PCBs according to design specifications.
Working with Gerber Files
Working with Gerber files requires specialised tools and software to view, analyse, and interpret the data for PCB manufacturing. These tools allow designers and manufacturers to inspect each layer of the PCB design and ensure accuracy before production begins.
Tools and Software for Viewing Gerber Files
Several software tools are available for viewing and editing Gerber files. Popular options include:
- GerbView: A widely used viewer that supports multiple formats and allows detailed inspection of layers.
- KiCad: An open-source PCB design tool that also features Gerber file viewing.
- Altium Designer: A professional-grade PCB design software offering comprehensive Gerber file export and analysis tools.
- Online Gerber Viewers: These cloud-based platforms allow for quick viewing without installing software.
Steps to Analyze and Interpret Gerber Data
- Import the Gerber Files: Load the Gerber files into the viewing software. Typically, each file represents a different layer (e.g., copper layers, solder masks, drill files).
- Inspect Each Layer: Inspect each layer individually to check for issues such as misaligned traces, missing drill holes, or cold solder joints. Cross-referencing layers ensures that everything is correctly aligned.
- Check Design Parameters: Confirm that the apertures, trace widths, and hole sizes match the design specifications. The software allows you to zoom in for precision checking.
- Run DRC (Design Rule Check): This feature automatically checks for design violations, such as trace spacing issues or unconnected nets, ensuring that the design adheres to manufacturing tolerances.
Common Issues and Troubleshooting Tips
- Misalignment of Layers: Ensure all layers are aligned correctly in the viewer before sending files to the manufacturer. If misaligned, check the origin points and units used.
- Missing Data: Occasionally, data such as drill files might not be exported correctly. Double-check the export settings to ensure all necessary files are generated.
- Incorrect Aperture Definitions: If apertures appear incorrectly, verify that the aperture list was embedded correctly during export.
By using the right tools and following these steps, designers can work effectively with Gerber files, ensuring that their PCB designs are production-ready.
Generating Gerber Files Using PCB Design Software
Generating Gerber files is a crucial step in PCB design, as these files directly guide the manufacturing process. The process varies slightly across different PCB design software, but the general principles remain consistent. Tools such as Altium Designer, Eagle, KiCad, and EasyEDA all support Gerber file generation.
Process of Generating Gerber Files with Various PCB Design Tools
- Design Finalisation: Before generating Gerber files, the PCB design must be completed, including all necessary layers such as copper traces, solder masks, silkscreens, and drill holes. Ensure that the design follows manufacturing guidelines to prevent errors during fabrication.
- Exporting Gerber Files:some text
- Altium Designer: Navigate to File → Fabrication Outputs → Gerber Files, select the layers to be exported, configure the units and format (RS-274X is recommended), and generate the files.
- KiCad: From the PCB layout editor, select Plot, choose the Gerber format, and specify the layers for export, including additional files like drill and edge cuts.
- Eagle: In the PCB layout editor, use the CAM Processor tool to select the Gerber format and the required layers and then generate the files for each layer.
- EasyEDA: Go to Fabrication Output and select the Gerber export option to ensure all necessary layers are included.
Ensuring Accuracy and Completeness in Generated Files
The accuracy of the generated Gerber files must be checked. In most software, a Gerber viewer is built-in that can be used to check the files. Thoroughly examine all layers for completeness and make sure everything is correct, that include traces, pads, drill holes and silkscreen details. Also, it can avoid any design violations by running a Design Rule Check (DRC) prior to export.
Design and Manufacturing Workflow integration
After Gerber files have been created and checked, they are usually utilised within the context of a complete design-to-manufacture flow. These files are then given to the PCB manufacturer (along with a BOM and sometimes pick-and-place files for assembly.) That is why the Gerber files have to be perfect and validated well before production to avoid any deviances from design-to-fabrication transition. This integration in turn minimises the need for costly changes or delay further down the line.
Naming and Managing Gerber Files
In the manufacture of PCB, the Gerber files should be named and managed properly to help factories recognize it conveniently as well as interpret them correctly. By following standardised naming conventions, not only would there be less confusion but the line of communication between designer and fabricator is improved.
Guideline to Naming and Organizing Gerber Files
A clean and organised naming convention is key to managing Gerber files efficiently. There will be a number of Gerber files that represent different layers or tasks in the PCB layout and those names should indicate what they represent. For example, a common approach is to use descriptive labels such as:
- Top Copper Layer: PCB_Top_Copper.gbr
- Bottom Copper Layer: PCB_Bottom_Copper.gbr
- Top Solder Mask: PCB_Top_SolderMask.gbr
- Bottom Solder Mask: PCB_Bottom_SolderMask.gbr
- Drill File: PCB_Drill.gbr
- Board Outline: PCB_Outline.gbr
Name file, including the name of the layer, it will be very simple to find and organise them into a project folder. While most PCB design tools will automatically generate these filenames based on the layers, at certain times a manual naming needs to be done.
Standardised Naming Conventions Are Important
Because it becomes standardised, naming is important for helping to maintain consistency and understanding as a product travels through the manufacturing process. Clear and descriptive names help avoid mistakes in layer interpretation when sending files to manufacturers. For instance, if the top and bottom copper layers are misidentified board would be either defected or late delivered. They called it a standard, because having standardised names makes changing and reviewing the intent easier for others on the team.
In addition, to enable their own processes manufacturers often need Gerber files in a specific naming convention. Manually having to find the correct documents for each layer and during every phase of manufacturing in order is no longer a hassle if all these files are given clear, descriptive names to prevent miscommunication from one team member to another.
Handling File Extensions and Format Variations
Gerber files typically have a .gbr extension, though some variations exist depending on the software and version used. Older Gerber formats, such as RS-274D, may use separate aperture files with a .apt extension, while the newer RS-274X format embeds the aperture data within the Gerber file itself.
Drill files, while part of the Gerber suite, are often generated as separate files with a .xln or .drill extension. It is essential to ensure that these files are included with the Gerber package, as they provide crucial information for drilling holes in the PCB.
The only thing is that while working on lots of different projects and overseeing many Gerber files standards may start to get mixed up. When it comes to output, some design tools may need files in a kind of configuration for them (the file) to be recognisable as required by the manufacturing software.
Organizing Project Folders
Organising all Gerber files in a separate folder having the project's name and version is another great way of managing. For the projects which are massive and broad, subfolders can be employed so as to maintain files collectively under layers or functionality of them.
By paying attention to these naming and organisational details, designers can keep their Gerber files organised well which will prevent mistakes down the line, make it easier for others to collaborate with them on projects or step in if they are suddenly unavailable during different stages of PCB production.
Documentation and Post-Generation Processes
Gerber files and documentation go hand-in-hand to fill in every gap relating to an order. Good documentation helps designers and manufacturers communicate more clearly so that all necessary demands are met, lowering the margin of production errors.
The Role of Documentation Post Gerber File Generation
The documentation itself acts as a reference for both the PCB designer and manufacturer. It clearly explains the function of each file in the Gerber and ensures correct manufacture for every layer of PCB. When files are poorly documented during manufacturing, the file data can be misinterpreted by manufacturers, causing defects in the final product. Moreover, documentation functions as a necessary safeguard for how design evolves through revisions and adherence to quality control in compliance with regulations.
Common Practices for Documenting Gerber Files
- Layer Stack-up Description: This provides the order and materials of PCB layers. It defines the copper weight, dielectric stuff and order of routing layers to let the manufacturer know what is configured physically on board.
- Assembly Drawings: Placement of wax on PCB. These are the drawings that help manufacturers to place components during layout stage and these specs would be normally accompanied with Gerber files.
- Drill Chart and Details: A drill chart detailing the necessary drill sizes, tolerances, as well as locations in relation to Gerber files. The whole location for the components and vias are absolute.
- README file: Include a README or fabrication notes that provide a summary of the Gerber files, production instructions and pertinent information about the board. Specifying with estimation impedance control needs or selective surface finishes will also help in avoiding misinterpretations.
Matching Documentation with Gerber File Specifications
All documentation should be consistent with the data in the Gerber files to prevent discrepancies. Any discrepancy between the files and documentation can result in production delays or eligibility of defects. This helps to reduce manufacturing errors by making sure that documentation is in line with the Gerber file specifications, which can make PCB fabrication a more efficient and accurate process.
Conclusion
Gerber files are the most broadly used means of communicating detailed design information within the PCB fabrication process, — this is all just formatted data and even houses everyone's lovely Trump jokes. They define everything from copper layers and drill holes to solder masks, which prevent errors during the fabrication of circuit boards. Best practices such as these using standardised naming conventions, accurate file verification, and thorough documentation can greatly reduce the risk of manufacturing errors (therefore increasing efficiency).
Over the years, with advancements in PCB technology, Gerber file formats have also evolved to support more complex design files and manufacturing techniques. These are further automation, which is normal for most industries and will interface with what future fabrication technology offers in easy compatibility with Gerber files, making the file type useful far into the horizon. Designers and customers alike need to be aware of these if they are to ensure high quality standards for the manufacturing process that inspire innovative breakthroughs.
Table of Contents
What is Gerber Files ?
The History and Evolution of Gerber Files
Gerber Files as ASCII Text Files
The Role of Gerber Files in PCB Manufacturing
How Gerber Files Guide the Manufacturing Process
Data and Structure in Gerber Files
How Data is Used to Create PCB Boards
Understanding the Structure of Gerber Files
Working with Gerber Files
Generating Gerber Files Using PCB Design Software
Naming and Managing Gerber Files
FAQs :
1. What are Gerber files and why are they important?
Essentially, Gerber files are the standard file format for PCB (Printed Circuit Board) fabrication, used to identify specific layers of a PCB design. These are an important set of files, as they contain information regarding the copper traces, solder masks and silkscreen along with drill holes on a given board. These Gerber files are digital blueprints that guide manufacturers how to realise accurate and precise PCBs. They play a role in ensuring the design intent is distinctly communicated, and every process from etching to drilling is accurately executed every time.
2. How do I view and analyse Gerber files?
To view and analyse Gerber files, use GerbView which is a good free viewer for the format or other tools like KiCad, Altium Designer along with online viewers to get detailed information. By giving process engineers visibility of each PCB layer, these tools allow them to view created details (such as copper traces, drill holes and silkscreen components) so they can verify the design from manufacturing view point. Users can load the Gerber files into this software, zoom in to specific regions of interest,(ie vias as an example), cross-check for design rule compliance and possible errors before releasing files onto production. Testing the fitment of concept design to maintain its accuracy before manufacture.
3. What are the essential Gerber files needed for PCB production?
Required Gerber files in PCB production are; Copper Layer Files, Solder Mask Files (SILK), Silkscreen File and Drill file. The copper layer files show where the traces and pads need to go, while the solder mask shows the areas that should have no solder resistance. The silkscreen files, however, contain the data necessary for labelling of components (component identifiers), whereas drill files give coordinates and sizes by reference to all holes which need to be placed in PCB. Even more separately files are needed for multi-layer boards, with a different file for each layer and an outline defining the shape and size of the PCB. Every file is mandatory for correct production.
4. How can I manage and name my Gerber files effectively?
Effective management and naming of Gerber files involve using standardised and descriptive file names that clearly identify the purpose of each file, such as Top_Copper.gbr or Drill_File.xln. Organising the files in dedicated project folders with subfolders for different layers or functions can help streamline the process. Consistent naming conventions reduce the risk of confusion during production and ensure that both designers and manufacturers can easily locate and interpret the files. It's also essential to keep backups of the files and document their structure and content for future reference.
5. What should I do after generating Gerber files?
Once the Gerber files are produced, it is then a case of documenting this output and checking that they correspond with how the PCB has been designed. This involves creating a layer stack-up description, drill charts and assembly drawings; additionally including a readme file to provide an overview of the files along with information that has been requested by the manufacturer. Also review files using a Gerber viewer to ensure they are both complete and correct. After the verification, these files are seamlessly merged with dozens of other manufacturing documents so that they can be used for production without any risk.