FR4 PCBs have emerged as the industry standard of the modern electronics industry. FR4 provides outstanding mechanical strength and insulating properties from a woven fiberglass cloth with an epoxy resin binder. The "FR" designation indicates that the material is flame retardant, so it is appropriate for many different demanding uses.
Industries including consumer electronics, automotive, aerospace, and telephony make great use of FR4 PCBs. Everything from cellphones and laptops to vehicle control systems and satellites has them present. Their adaptability and strength define many electrical devices as their backbone. Excellent mix of performance, cost-efficiency, and material qualities makes FR4 popular in PCB manufacture. Long-lasting circuit boards are guaranteed by FR4's resistance to moisture and chemicals as well as by its resilience in different temperatures and surroundings.
Its low cost relative to other high-performance materials also makes it a favourite choice for producers trying to generate dependable, reasonably priced PCBs. Generally speaking, FR4 PCBs are essential for the flawless running of innumerable electronic products and systems all around since they highlight the exceptional material performance and usefulness in many different fields.
Key Highlights
- FR4 is a grade classification for a kind of material used in PCB manufacture that consists mostly of woven fiberglass.
- Some of the key properties of FR4 PCBs are signal integrity, dielectric strength, mechanical reliability, and resistance to harsh environment conditions.
- You must assess performance requirements, budget, frequency, and environmental concerns before choosing a FR4 PCB.
- FR4 is a popular choice for PCBs due to its cost-effectiveness and versatile performance, but it has limitations when it comes to handling heat.
- The main types of FR4 PCBs are Standard FR4, High-Tg FR4, FR4 with High CTI, FR-4 Rogers Hybrid, and Flexible FR4.
What Is FR4 and Its Meaning?
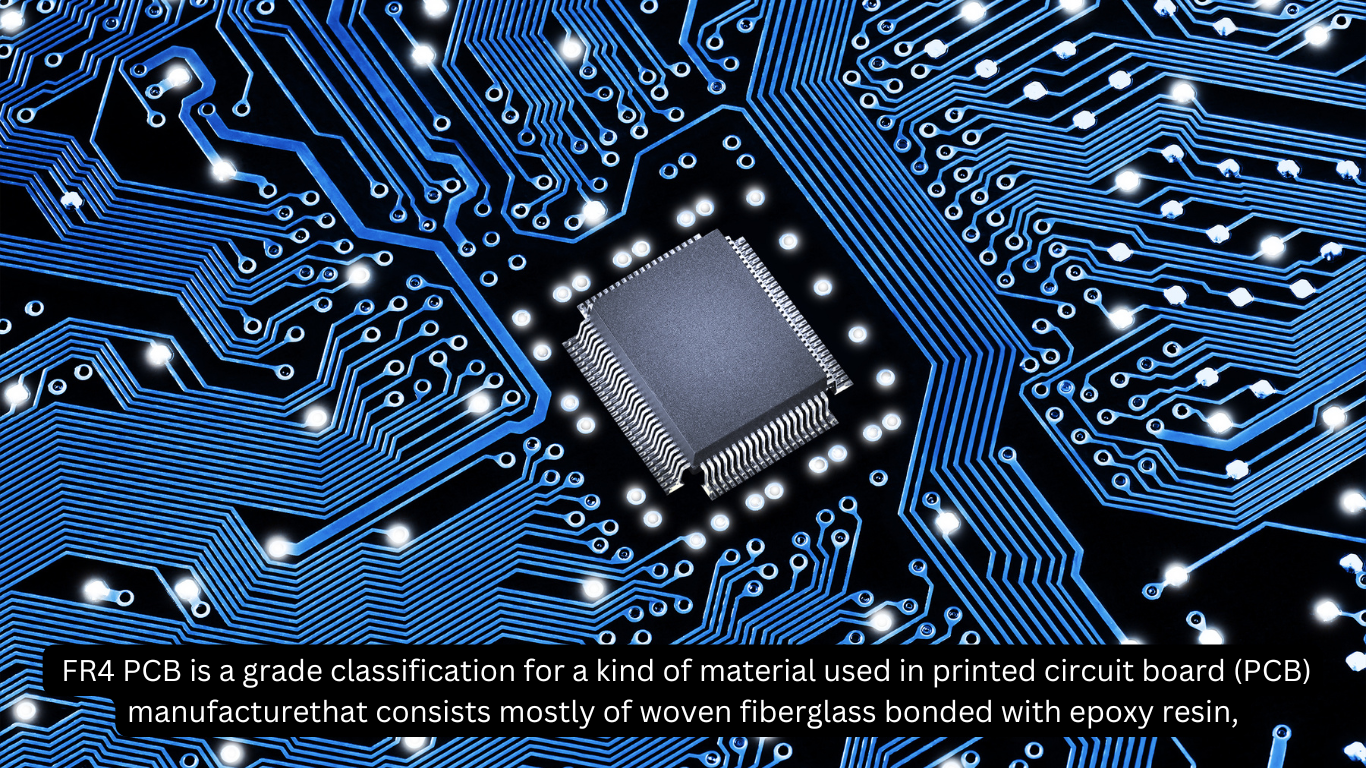
Short for "Flame Retardant 4," FR4 is a grade classification for a kind of material used in printed circuit board (PCB) manufacture. It consists mostly of woven fibreglass bonded with epoxy resin, which provides great mechanical strength and electrical insulation.
With FR4 becoming the most often used due to its better qualities, the "4" in FR4 distinguishes this material from previous types of flame-retardant materials. FR4 originated in the middle of the 20th century as synthetic resins and fibre-reinforced materials were being developed. A material that could not only support sophisticated circuitry but also resist fire and survive high temperatures was increasingly needed as electronic gadgets got more complicated. This resulted in the 1960s FR4 invention, which offered a dependable, long basis for PCB manufacture.
Historically, FR4's invention represented a major breakthrough in electronics since it made more compact, high-performance circuit boards able to run safely under various environments. Ensuring the safety and lifetime of electrical gadgets depended primarily on the material's fire-resistant properties. Thanks in part to its mix of cost, performance, and safety, FR4 is still the favoured material for PCB manufacture today.
Key Properties of FR4 Substrate Material
Excellent physical and chemical characteristics of FR4 substrate material make it a top choice for PCB manufacture. Check out them:
- Dielectric strength is one of its main characteristics since it offers strong electrical insulation with a high dielectric constant of over 4.5.
- Has a signal integrity over several layers of the PCB and lets FR4 stop electrical interference. Still another defining quality of FR4 is thermal stability. Its high glass transition temperature (Tg) of roughly 130–140°C means it stays stable and structurally sound even at high temperatures. This qualifies FR4 for settings like automotive and aerospace electronics where heat stress is a consideration.
- FR4 shows great mechanical strength, therefore guaranteeing the board's durability and rigidity even under physical force or vibrations. These characteristics together affect the performance of FR4 in PCBs by allowing the material to manage complicated circuitry and guarantee long-term dependability.
- Its resistance to moisture, chemicals, and environmental conditions guarantees constant operation of the circuit boards over several uses. Moreover, FR4's balanced mechanical, thermal, and electrical characteristics enable it to satisfy the needs of several sectors and preserve mass production's affordability.
Exploring the Variations in FR4 Material Properties
Because of variations in manufacturing techniques, resin compositions, and quality control methods, FR4 material qualities can vary greatly amongst producers. Though FR4 usually follows a standard specification, manufacturers may create small variances that affect its mechanical, thermal, and electrical performance. The dielectric constant (Dk) of FR4 is one of the main differences seen across several producers.
Although the normal Dk for FR4 is about 4.5, manufacturers may create materials with somewhat different Dk values depending on the resin composition and the fibreglass weave employed. Particularly in high-frequency applications where uniformity in dielectric characteristics is crucial, these variants can affect signal transmission quality.
Varying FR4 products are thermal characteristics including glass transition temperature (Tg). Certain producers might improve their FR4 material to resist more temperatures, producing variations with Tg values above 170°C. Applications needing improved thermal stability, including those in automotive electronics or power devices, depend on these fluctuations, which are usually attained by changes in the epoxy resin mix. The homogeneity and dependability of FR4 characteristics are strongly influenced by manufacturing techniques and quality management.
Final material qualities can be influenced by elements like laminating pressure, fibre weave tightness, and resin curing. For example, differences in thickness or surface quality resulting from unequal resin application during the laminating process will affect the mechanical strength and general lifetime of the PCB. Different manufacturers have different quality control policies which result in differences in mechanical strength, moisture resistance, and flame-retardant qualities. While lower-grade materials may show poor performance in harsh conditions, high-quality FR4 substrates are tested to guarantee they satisfy industrial criteria.
Choosing the appropriate FR4 material ultimately requires an awareness of these variances and a selection of producers with a track record of producing consistently high-quality goods that satisfy the particular needs of your application.
FR4 Circuit Board Materials: Limitations and Key Considerations
Although FR4 is generally utilised in PCB manufacturing because of its adaptability and economy, its limitations should be taken into account for certain uses. The main limitation of FR4 is its sensitivity to moisture absorption. Although it has some degree of moisture resistance, extended exposure to wet surroundings might reduce its electrical performance, therefore causing signal integrity problems or short circuits.
Unless appropriate protective coatings are used, this restriction renders it less fit for outdoor or high-humidity uses. FR4's thermal performance presents still another constraint. Standard FR4 materials have a glass transition temperature (Tg) of roughly 130–140°C, which makes them inappropriate for high-temperature situations like car power electronics or industrial equipment even if their thermal stability is rather good. In these situations, dependability is ensured by using high-Tg FR4 versions or other materials such as polyimide. Additionally lacking the thermal conductivity required for uses including notable heat dissipation, such in high-power LEDs or RF circuits, is FR4. If not properly controlled through design factors like heat sinks or thermal vias, its low thermal conductivity can create hot patches that cause component early failure. Using FR4 in various contexts has practical issues including balancing cost and performance.
FR4 offers a great answer for low to medium-complexity circuits with limited exposure to harsh conditions. Standard FR4's dielectric characteristics can become problematic for high-frequency circuits, though, and cause signal loss or interference. For these situations, designers would have to choose more advanced materials like Rogers laminates or specialist FR4 materials with ideal dielectric constants.
Furthermore in applications needing flexible circuits, FR4's stiff character becomes a constraint. Other materials like flexible polyimide substrates must be taken into account for designs requiring bending or flexing. In essence, even although FR4 is flexible, best performance in certain uses depends on knowing its limitations and choosing the suitable variation or alternative material.
Tips for Choosing the Ideal FR4 Material for Your PCB
Choosing the ideal FR4 material for your PCB depends on balancing the cost and the specific requirements of your application. Here are some essential tips to guide you through the selection process.
1. Assess Performance Requirements: Consider the electrical and mechanical needs of your project. For most general-purpose electronics, standard FR4 will suffice as it offers a good balance of mechanical strength and electrical insulation. However, if your application involves higher operating temperatures, such as in automotive or industrial settings, you may need high-Tg FR4, which can withstand temperatures above 170°C without degrading.
2. Evaluate Cost vs. Application: FR4 is known for being cost-effective, but within the category, prices vary depending on performance grades. Standard FR4 is ideal for budget-conscious projects with low to moderate complexity. But when dealing with high-frequency circuits or harsh environments, investing in higher-quality FR4 with enhanced dielectric properties or improved moisture resistance is often worth the additional cost. Evaluate how much performance you need and avoid overpaying for advanced variants unless necessary.
3. Consider Frequency and Signal Requirements: For high-frequency applications, such as in telecommunications or RF circuits, standard FR4 may not be the best choice due to its higher dielectric constant, which can cause signal loss or interference. In these cases, consider an FR4 material with a lower dielectric constant or alternative substrates specifically designed for high-frequency use.
4. Environmental and Moisture Concerns: If your PCB will be used in environments prone to moisture or extreme temperatures, consider FR4 variants with enhanced moisture resistance or the application of protective coatings. Pay attention to how your material choice performs under environmental stress, especially in outdoor applications.
5. Thickness and Layer Count: Consider the thickness of the FR4 material and the number of layers required for your PCB design. Thicker FR4 substrates provide greater mechanical stability but may limit flexibility in multilayered designs.
The Role of FR4 in PCB Manufacturing
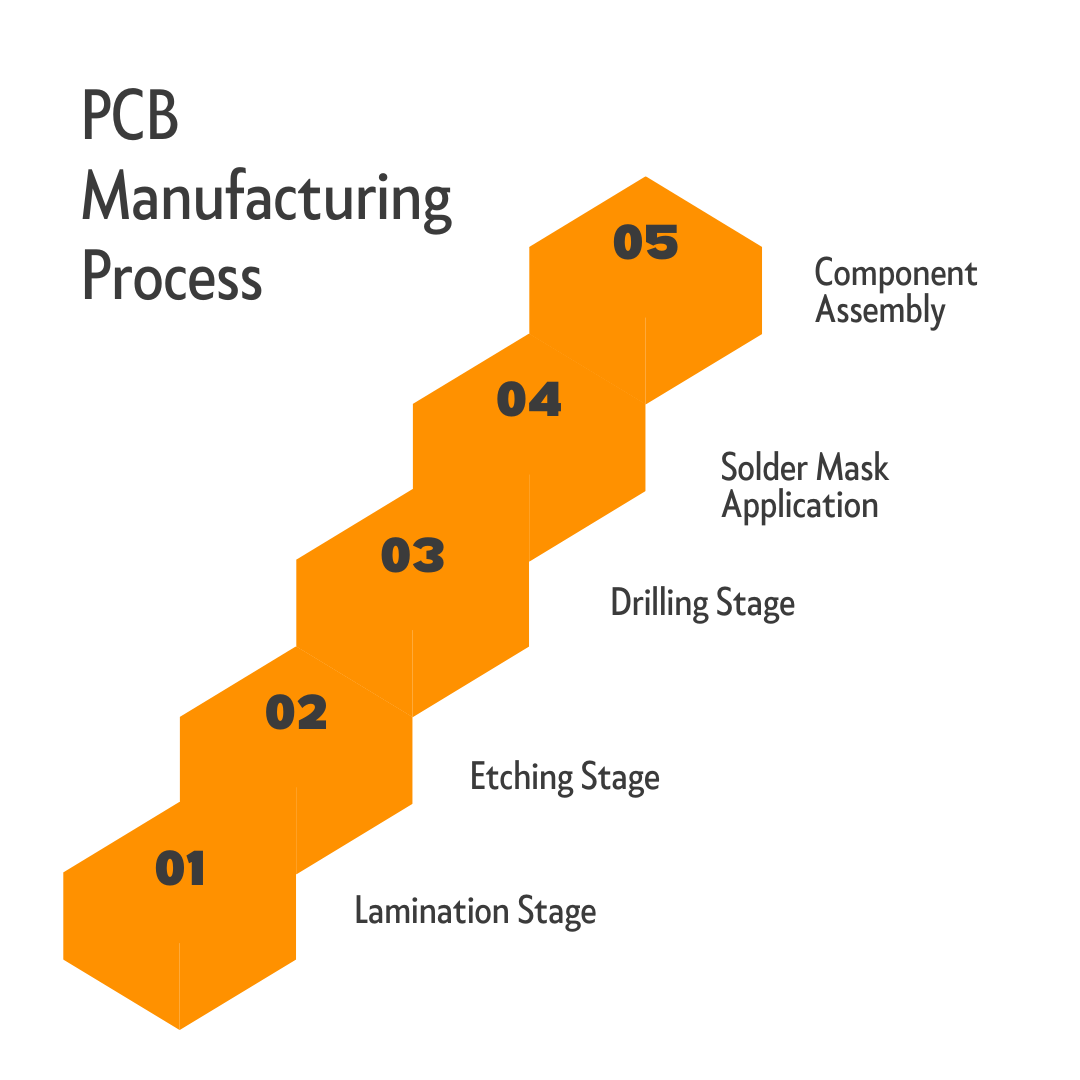
FR4 plays a crucial role in PCB manufacturing, serving as the core substrate material that provides the foundational support and insulation for electronic circuits. Its versatility and cost-efficiency make it the most widely used base material in the industry.
- Lamination Stage: The manufacturing process involving FR4 begins with the lamination stage, where sheets of FR4 material, typically consisting of woven fibreglass cloth and epoxy resin, are layered together to create a rigid base. Copper foil is laminated onto both sides of the FR4 substrate, forming the conductive surface for circuit paths. The lamination process is conducted under heat and pressure to bond the layers together securely.
- Etching Stage: Now, the copper layer bonded to the FR4 substrate is selectively removed to create the desired circuit patterns. A chemical PCB etching process removes excess copper, leaving only the required copper traces that will conduct electricity between components on the board. Throughout this process, the FR4 substrate maintains its mechanical integrity, ensuring that the board remains durable and resistant to stress.
- Drilling Stage: Holes are drilled into the FR4 substrate to allow for component mounting and electrical connections between layers. FR4's rigidity and strength ensure clean, precise holes, preventing cracking or delamination. Once the holes are drilled, they are typically plated to enable conductivity between different layers of the PCB.
- Solder Mask Application: A protective layer is added to the copper traces to prevent short circuits and protect the board from environmental factors. The FR4 substrate plays a key role in providing stability during this phase, allowing for consistent application of the solder mask.
- Component Assembly: Finally, electronic components are mounted onto the etched and drilled FR4 PCB, followed by soldering to establish electrical connections. FR4’s thermal and mechanical properties ensure that the board remains robust throughout the soldering process, preventing warping or damage.
Choosing the Right FR4 Thickness for Your PCB
Choosing the right FR4 thickness is a critical step in PCB design, as it directly impacts both the electrical and mechanical performance of the circuit board. FR4 thickness, which typically ranges from 0.2 mm to over 3.2 mm, determines the board's rigidity, signal integrity, and heat dissipation capabilities, making it a key consideration during the design phase.
1) Electrical Considerations
The thickness of the FR4 material can influence the electrical characteristics of the PCB pad. Thicker boards generally have better insulation properties, which can help in reducing electromagnetic interference (EMI) and improving signal integrity, particularly in multilayered or high-frequency designs. On the other hand, thinner boards may be more suitable for applications where compact size is crucial, such as in mobile devices or wearables, but may sacrifice some performance in terms of signal isolation.
2) Mechanical Considerations
The mechanical strength of the PCB is another factor closely tied to FR4 thickness. Thicker boards offer greater rigidity and can withstand mechanical stress better than thinner boards, making them ideal for applications involving heavy components, mechanical vibrations, or environmental stress, such as automotive or industrial electronics. However, thicker PCBs may limit design flexibility in terms of routing complexity and the number of layers.
Tips for Selecting the Optimal Thickness
- Application Requirements: If the PCB will be used in high-frequency or high-power applications, consider a thicker FR4 substrate to improve electrical performance and manage heat dissipation. Thicker boards also provide added stability for large or heavy components.
- Size Constraints: For devices where space is a premium, such as in consumer electronics or wearables, thinner FR4 materials may be preferred. However, you should ensure that the thin substrate still meets the mechanical requirements of your application.
- Layer Count: Multilayer PCBs often use thinner FR4 substrates to accommodate additional layers without increasing the overall board thickness excessively. For single-layer or double-layer boards, thicker substrates are more common.
When Is FR4 the Best Choice for PCB Material?
In situations where cost-effectiveness, adaptability, and durability rule, FR4 is the greatest option for PCB stencil material. It shines in settings where modest mechanical and electrical performance is required without the great demand of high-frequency or high-power applications. For a wide spectrum of typical electronic goods, FR4 is perfect because of its capacity to balance cost with acceptable thermal, mechanical, and electrical characteristics. For instance, FR4's dependability and economy help consumer gadgets including computers, cellphones, and home appliances.
For most digital circuits, its modest dielectric constant offers enough signal integrity; its thermal stability guarantees durability in usual running conditions. Where its mechanical robustness and flame-retardant qualities are vital, FR4 also shines in automotive and industrial control systems. FR4 with protective coatings can still work well in settings requiring moisture resistance, such those of outdoor devices or humid situations. Furthermore benefiting from FR4's capacity to manage heat while preserving structural integrity include telecommunications equipment, instrumentation, and power supply running under mild thermal stress.
Managing Heat with FR4 PCBs
FR4 is a popular choice for PCBs due to its cost-effectiveness and versatile performance, but it has limitations when it comes to handling heat. FR4 has a moderate glass transition temperature (Tg), typically ranging from 130°C to 170°C for standard and high-Tg variants. This defines the point at which the material begins to lose its rigidity and mechanical integrity under thermal stress. However, while FR4 offers reasonable thermal stability for many applications, it has low thermal conductivity, making it less effective at dissipating heat compared to more specialised materials.
To manage heat in FR4-based PCBs, several strategies can be implemented to enhance thermal dissipation and maintain performance:
- Copper Planes and Heat Sinks: Incorporating copper planes within the PCB assembly can improve heat conduction away from critical components. The thicker the copper layer, the better the heat transfer. Additionally, external heat sinks can be mounted on the PCB to further dissipate heat away from the board, keeping temperatures within acceptable ranges.
- Thermal Vias: Using thermal vias is another effective method for improving heat dissipation in FR4-based PCBs. These vias connect the top and bottom layers of the board, allowing heat to transfer between layers and spread more evenly across the PCB. They are especially useful in multilayer designs where heat buildup can be concentrated in certain areas.
- Component Placement: Proper component placement is essential for managing heat in FR4 PCBs. Placing heat-sensitive PCB components away from high-power, heat-generating components can reduce localised hotspots. In addition, spreading out power-dissipating components ensures that heat is distributed more evenly.
- Thermal Interface Materials: Using thermal interface materials (TIMs) such as thermal pads or pastes between components and the PCB helps improve thermal contact, facilitating better heat transfer and lowering component temperatures.
FR4 vs. High-Frequency Laminates: How to Make the Right Choice
Choosing between FR4 and high-frequency laminates depends on the specific performance requirements of your PCB application, particularly in terms of signal transmission, thermal management, and cost considerations.
Performance and Suitability
FR4 is widely used for general-purpose PCBs due to its cost-effectiveness and balanced performance in moderate-frequency applications. It has good mechanical strength, decent electrical insulation, and moderate thermal stability. However, its dielectric constant (around 4.5) and loss tangent make it less suitable for high-frequency applications, especially those above 1 GHz, as signal degradation can occur due to its inability to efficiently handle high-speed signals.
High-frequency laminates, such as Rogers or PTFE-based materials, are specifically designed for high-speed, high-frequency applications like RF circuits, microwave systems, and telecommunications. These materials have lower dielectric constants (typically below 3.5) and much lower loss tangents than FR4, enabling better signal integrity, reduced signal loss, and superior high-frequency performance.
Pros and Cons
FR4 Pros
- Cost-effective for low to moderate-frequency applications.
- Adequate thermal and mechanical performance for most consumer and industrial electronics.
- Readily available and widely supported in PCB fabrication processes.
FR4 Cons
- Poor performance in high-frequency applications, causing signal attenuation and interference.
- Limited thermal conductivity, making it less suitable for high-power or high-heat designs.
High-Frequency Laminates
Pros
- Excellent signal integrity at high frequencies due to lower dielectric constants and loss tangents.
- Superior thermal performance, making them suitable for high-power and RF applications.
- Reduced signal degradation and better impedance control.
Cons
- More expensive than FR4, which can be cost-prohibitive for lower-end applications.
- May require specialised fabrication processes and design expertise, increasing production complexity.
For general-purpose electronics, FR4 offers a cost-effective and reliable solution. However, if your application involves high-frequency signals, RF circuits, or microwave technologies, high-frequency laminates are the superior choice, offering improved signal performance and thermal management at a higher cost.
Top Benefits and Essential Properties of FR4 Material
Because of its well-rounded advantages and characteristics, FR4 is the most often used material for the PCB fabrication process. Excellent balance of performance and cost-efficiency is one of FR4's main benefits. It guarantees exceptional mechanical strength and strong electrical insulation, thereby assuring that PCBs stay dependable over extended times.
Denoted by the "FR" mark, its flame retardant qualities make it a safe choice for many electronic uses since they stop the spread of fire in case of component failures or too high temperatures. FR4's thermal resilience is another major advantage since it lets it operate in conditions with little thermal stress.
Low to moderate-frequency uses find the material appropriate as its great dielectric strength guarantees strong signal integrity and lowers the possibility of electrical interference. Furthermore quite flexible and able to be used in single-layer, double-layer, and multilayer PCBs, FR4 allows a broad spectrum of designs. Its resilience to external elements, chemicals, and moisture improves still another level.
Different Types and Grades of FR4 Available
FR4 comes in various types and grades, each tailored to specific applications and performance requirements. These variations primarily differ in thermal, electrical, and mechanical properties, making it essential to choose the right FR4 type based on your design needs.
1) Standard FR4
The most common type, standard FR4, is used in general-purpose applications. It has a glass transition temperature (Tg) around 130-140°C, which is sufficient for most consumer electronics, industrial equipment, and automotive controls. Standard FR4 provides a good balance of cost and performance, making it ideal for low to moderate-frequency applications and single or double-layer PCBs.
2) High-Tg FR4
High-Tg FR4 has a higher glass transition temperature, typically above 170°C. This type is designed for applications that operate in higher thermal environments, such as automotive electronics, power supplies, and industrial equipment exposed to elevated temperatures. High-Tg FR4 maintains its rigidity and performance in harsher conditions, preventing warping or delamination, which is crucial in high-reliability designs.
3) FR4 with High CTI (Comparative Tracking Index)
This grade of FR4 features enhanced electrical insulation properties and is ideal for high-voltage applications. The increased CTI rating provides better resistance to electrical tracking, making it suitable for power supplies, motor controllers, and other circuits where high voltage and potential arc risks are present.
4) FR4-Rogers Hybrid
For applications requiring both the affordability of FR4 and the superior high-frequency performance of Rogers laminates, hybrid boards are available. These combine the properties of both materials, allowing cost-effective solutions for RF and microwave applications without compromising signal integrity. This is commonly used in telecommunications and high-frequency circuits where maintaining signal quality is critical.
5) Flexible FR4
Some variations of FR4 are designed to offer slight flexibility, making them useful for applications where the PCB needs to conform to a specific shape or endure limited bending, though this type is less common than flexible polyimide materials.
When To Avoid Using FR4 in PCB Design?
Although FR4 is a flexible material, not every PCB design will find it appropriate. High-frequency PCBs like RF and microwave circuits are one instance when FR4 is not advised. Operating over 1 GHz FR4 is inappropriate for designs since its dielectric constant and loss tangent generate notable signal attenuation and interference. In these situations, better appropriate materials are Rogers laminates or PTFE-based substrates, which have lower dielectric constants and enhanced signal integrity.
Furthermore unsuitable for high-power or high-heat situations is FR4. Its glass transition temperature (Tg) at 130–140°C and modest thermal conductivity render it prone to thermal failure in such conditions. Materials like aluminum-backed PCBs or high-Tg FR4 variations provide better thermal management for uses including severe heat dissipation, including power electronics, LED boards, or industrial systems.
At last, FR4 is not the ideal option for flexible circuits or situations needing notable bending or folding. Under these conditions, adaptable materials such as polyimide offer the required durability and flexibility without delamination or cracking.
The Importance of FR4 in PCB Design and Its Industry Impact
Because of its adaptability, dependability, and economy, FR4 has had a significant effect on PCB design and the electronics sector. FR4 is the most often used PCB substrate material since it offers a strong mix between mechanical durability, electrical insulation, and thermal performance at a reasonable price range. From consumer products to industrial equipment, this is the backbone of many contemporary electronic tools.
Excellent dielectric qualities of FR4 are one of its significant contributions since they enable it to preserve signal integrity in low to moderate-frequency applications, therefore guaranteeing efficient operation and minimum interference in electronic circuits. In uses where dependability is vital, such automotive systems, telecommunications, and aircraft, its flame-retardant character and mechanical endurance also make it a safe and long-lasting choice.
Because FR4 performs consistently over a range of running circumstances, manufacturers can design PCBs that satisfy stringent safety and performance criteria without increasing costs. This has democratised manufacturing of electronics, therefore enabling the availability of sophisticated technologies in many sectors.
Conclusion
Because of its outstanding mix of cost, performance, and dependability, FR4 remains the most often used and flexible material in PCB layers production. From consumer electronics to industrial and automotive systems, FR4's excellent dielectric characteristics, thermal stability, and mechanical strength—which make it perfect for a broad spectrum of uses—are among the key aspects covered.
FR4's price and simplicity of fabrication make it the preferred choice for general-purpose PCBs even if it has restrictions in high-frequency, high-power, and flexible designs. FR4 gives manufacturers a strong basis for building dependable, robust PCBs that function in moderate environments. Knowing the particular needs of a project—such as those pertaining to thermal management, signal integrity, or environmental conditions—designers can select the appropriate FR4 variation or another material for best outcomes. FR4's adaptability and economy will always be mainstays of PCB manufacture.