Single-sided PCBs are the first printed circuit board technology, circulated in the 1950s and still running. These types of circuit boards have one layer of conductive metal. Copper is generally used to form this conductive layer. This layer is then laminated on a non-conductive substrate.
The biggest highlight of this circuit board is its simple design. It is the primary reason for the popularity of this board. Due to the no-complex layout, manufacturing errors drop a significant point, and producing it in bulk order becomes easy.
This article will guide the readers to know what is a single-sided PCB, from its definition to its design. So, keep reading till the end to better understand this compact yet powerful printed circuit board.
Key Highlights
- A single-sided circuit board features only one conductive layer, fixated in a non-conductive substrate.
- As a substrate, manufacturers mostly use fibreglass or phenolic resin. Copper, a popular conductor, has always been the primary choice for conductive layers.
- One of the key features of single-sided PCBs is their cost-effectiveness and compact design.
- Common applications, such as sensors, timers, calculators, and regular consumer electronics use single-sided PCBs.
- Due to their simple design, maintenance of single-sided PCBs is easy. Updating and modifications don’t require extensive work.
What Is A Single-Sided PCB?

Single-sided PCBs are one of the simplest forms of printed circuit board that features only one conductive layer, fixated in a non-conductive substrate. As a substrate, manufacturers mostly use fibreglass or phenolic resin. These two malleable materials provide structural integrity for the board.
Electronic components are soldered on one side of the circuit. On the other side, there will be conducting material. Copper, a popular conductor, has always been the primary choice for conductive layers. Then, there is a solder mask to protect it from short circuits. Along with that, there will be a silkscreen layer to add labels for component placement.
In all the common electronic devices, a one-sided PCB is used. It enables cost-effective production and strengthens reliability. For everyday appliances, this simple form of flex PCB plays a crucial role in boosting its efficiency and functionality.
However, there are a few downsides as well. Since these boards have only one conductive layer of metal, the electrical circuits can only be laid out on one side of the board. It also means that the conductive paths cannot cross or overlap each other. Thus, using single-sided PCBs leads to generally less efficient use of space compared to multi-layered PCBs.
Key Features
It is the features of single-sided PCBs that makes them unique. Have a look at some of them:
- Cost-effectiveness: They are easy to manufacture, which makes them inexpensive. And since it is only a one-layer circuit board, producing these boards in large quality becomes smooth and hassle-free. It is one of the reasons low-cost electronic devices choose single-sided circuit boards.
- Design: the design of this circuit board is another highlight of a single PCB. The simple layout can be easily produced in a mass volume. Even the PCB assembly process doesn't have any complexity. Thus, manufacturing this PCB requires less skill set in comparison to multi-layer PCB production.
- Application: Common applications, such as sensors, timers, calculators, and regular consumer electronics, do not require any complex circuit board. Thus, single-sided PCBs become a great addition to their designs. It also effectively contributes to reducing the cost and complexity of production.
As long as simple design becomes convenient for everyday electronic models, it comes with a few limitations as well. The one pcb layer of conductive paths does not allow space for crossover connections. Thus, it restricts the board from effective implementations of connecting to various PCB components. Designers require jump-wire to achieve the necessary crossover. Although, it may further complicate the assembly process of the circuit.
Benefits Of Single Sided PCB
Choosing single-sided PCBs offers multiple benefits. If used in the right manner, it reduces the production difficulty and boosts the efficiency of the product.
Here are a few benefits of using single-sided pcb:
- Cost-Effective Production: They are highly economical to design and create. In comparison to multi-layered PCBs, these styles require fewer materials and less processing. That's why the production cost is reduced. This cost efficiency makes them the best choice for high-volume production. For regular appliances, it saves a ton of money both for the producers and the consumers.
- Simplicity in Design and Manufacturing: The design process for single-sided PCBs is relatively straightforward. Thus, it reduces the time and expertise needed to create one layout. An easy design also makes manufacturing simple. Thus, it reduces production error in all verticals.
- Ease of Repair and Modification: Due to their simple design, maintenance of single-sided PCBs is easy. All the components are located on one side. Thus, accessing them for testing and repair doesn't become complicated. It also facilitates modifications and updates to the circuit board without extensive rework on multiple PCB layers.
- Ideal for Simple Applications: Everyday applications deserve a simple design, which is budget-friendly for the consumers and low-maintenance in nature. Single-sided PCBs are perfect for that reason. Be it LED lighting, power supplies, or consumer electronics, this single-layer circuit will enhance their functionality, without adding any complexity.
Single-sided PCB Design And Manufacturing
The single-layer PCB goes through multiple processes during its manufacturing and design time.
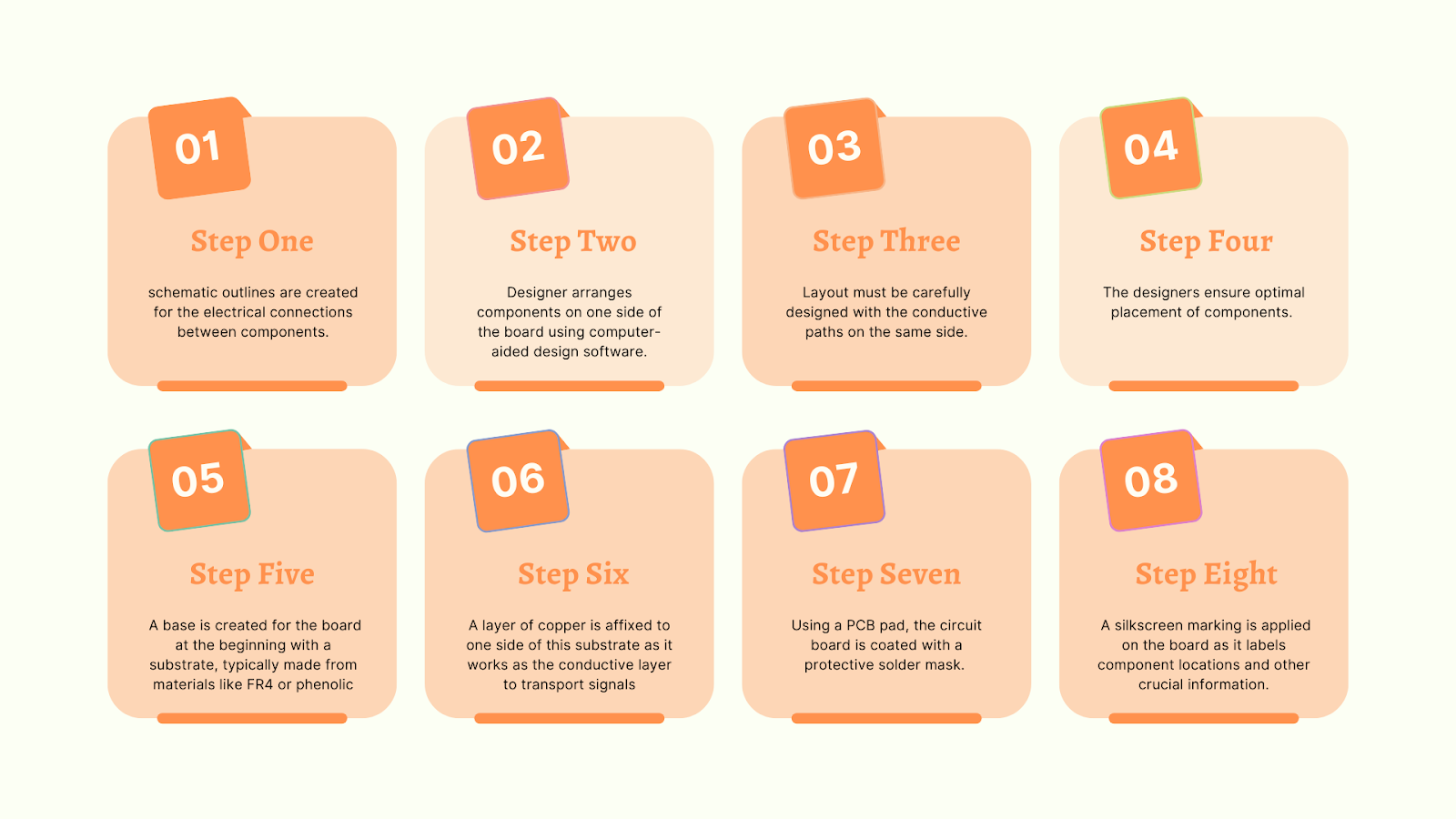
Design Phase
- During the design process, at first, schematic outlines are created for the electrical connections between components.
- Then the designer arranges components on one side of the board using computer-aided design software.
- This layout must be carefully designed. Thus, all conductive paths stay on the same side and cannot overlap. For crossover connections, designers generally use additional jump wires or similar solutions.
- Through these steps, the designers ensure optimal placement of components. It also minimises space requirements and maximises functionality.
Manufacturing Phase
- In the PCB fabrication process, a base is created for the board at the beginning. For that, a substrate, typically made from materials like FR4 or phenolic, is used.
- Then, a layer of copper is affixed to one side of this substrate. It works as the conductive layer to transport signals. Then chemicals are used in PCB etching on other areas. For smooth transpassing of signals, PCB gold fingers are also used.
- After that, using a PCB pad, the circuit board is coated with a protective solder mask. It helps prevent accidental solder bridges, which may happen during component soldering.
- At the end, a silkscreen marking is applied on the board. It labels component locations and other crucial information.
Single-Sided PCB Applications
Multiple appliances still use single-sided PCBs. Here are a few examples of them.
- Consumer Electronics: These types of circuit boards are commonly found in household electronic devices. From calculators to digital cameras, these devices require strength, durability and high functionalities. It is also noted that these applications don't require high-frequency pcb. Thus single layer pcb fulfils their circuit requirements.
- Power Supplies: Many basic power supply circuits also use single-sided PCBs. These boards suit the requirement of easy layouts. Power regulators, transformers, and capacitors often use such straightforward layouts. Thus, single-layer PCB provides a reliable platform for devices requiring power conversion and management.
- LED Lighting: LED applications, particularly those in lighting fixtures, often have simple circuitry involved. They are mostly cheap and require low-cost production. Thus, single-layer PCB boards are chosen.
- Automotive Components: In the automotive industry, single-sided PCBs are usually used in dashboard indicators, lighting systems, and other devices. These components do not require complex circuit designs. Thus single-sided PCBs become suitable for such applications. These boards also contribute to the durability of these automotive parts.
Industrial Applications: There are many control systems and sensors used in various industrial settings. These applications often select single-sided PCBs. These circuit boards are easy to accommodate and don't require high maintenance.
Design Tips For Single-Sided PCB
Designing any type of PCB, such as enig pcb, rf pcb or single-sided pcb requires strategic planning. To optimise the space and functionality of such boards, here are some tips:
- Maximise Layout Efficiency: Arrange components to minimise trace lengths. It will reduce potential interference and improve performance.
- Utilise Jumpers Sparingly: In this design, traces cannot cross. Hence, use jumpers wisely. It will avoid further complexing and cluttering the primary designs.
- Thorough Grounding: Focus on ensuring a solid ground plane. It will minimise electrical noise and enhance circuit stability.
- Opt for Larger Trace Widths: It will be able to handle more current. Also, the risk of trace damage will be reduced.
- Test Points Inclusion: Always include test points for troubleshooting. Thus, testing the functionality during and after assembly will be hassle-free.
- Use Surface-Mount Components: A pacing-saving model requires a compact design. Hence use surface mount components on the copper side with the help of a pcb stencil.
- Thermal Management: It is an essential feature. Identify heat-generating components. Then, ensure proper spacing among those components to avoid overheating.
Final Thoughts
To summarise, single-sided circuit boards have one conductive copper layer and a few other components like substrate, solder mask, and silkscreen. Their benefits, such as cost-effectiveness and simplicity, make them suitable for low-density designs and basic electronic devices. Understanding the design and manufacturing processes of circuit boards, such as Teflon pcb, ceramic pcb, Taconic pcb or any single-sided pcb, helps consumers make informed decisions.