Flex PCB refers to a flexible printed circuit board. Multiple circuits and components are mounted on a flexible substrate to create these boards. Modern applications are slowly demanding slimmer and flexible components, thus raising the importance of choosing flexible counterparts. But to fully understand what is Flex PCB, there are multiple PCB layers to uncover.
In this article, readers will get to know about Flex PCBs in detail, from their benefits, different types, where it can be used, understanding of their structure, and many more.
Key Highlights
- Flex PCBs are multilayer circuit boards used in electronic devices that use malleable materials like polyimide, polyester, or other polymers.
- Some of the common types of Flex PCBs are: single-sided flexible circuit, single-sided flexible circuit with dual access, double-sided flexible circuit, multi-layered flexible circuits, rigid-flex PCBs, and HDI PCBs.
- The layers of PCB are: conductive layer, dialectic substrate layer, adhesive layer, coverlay, and stiffeners.
- Some of the benefits of Flex PCB are space-saving, weight reduction, improved reliability and thermal management. However, it has significant disadvantages like higher initial costs, complexity, and repair challenges.
- Flex PCB is made up of polyimide, polyester, and adhesives.
- Flex PCB is used in consumer electronics, automotive industry, medical device, and aerial equipment.
What is a Flex PCB?
Flex PCBs are multilayer circuit boards used in electronic devices. Unlike traditional rigid PCBs, which are fixated on a stiff base, these modern PCBs use malleable materials like polyimide, polyester, or other polymers. It allows the Flex PCBs to bend smoothly, without breaking.
However, Flex PCBs are costlier than traditional PCBs. For instance, PCB gold fingers refer to gold-plated connectors at the edge of a PCB. But they offer significant advantages in applications where space and flexibility are the primary concerns.
Types of Flex Circuit Boards
Flex PCBs are divided into various types based on their layer functions:

1. Single-Sided Flexible Circuit Boards
A single-sided PCB consists of a single conductor layer. For that, typically copper is applied to a flexible polyimide film. Also, the conductor is only accessible from one side, making them suitable for simple, low-density applications.
2. Single-Sided Flexible Circuit Boards with Dual Access
In this type of PCB, the boards also have one conductor layer. But they feature access points on both sides of the substrate. Through PCB etching, more electrical pathways can be created. This allows for more complex connections without adding extra layers.
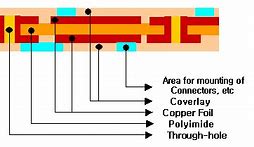
3. Double-Sided Flexible Circuit Boards
These boards have two conductive layers, one on each side of the flexible polyimide base. They accommodate more complex circuit designs and higher component density than single-sided boards.
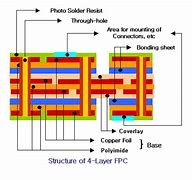
4. Multi-Layered Flexible Circuits
Several single and double-sided flex circuits are combined to create these PCBs for advanced electronic applications. The multi-layered boards use through holes or surface mounting to create dense and complex circuit configurations.
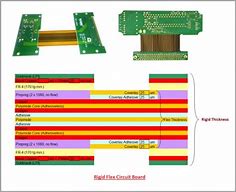
5. Rigid-Flex PCBs
These are hybrid boards merging flexible and rigid PCB technologies. This design allows for a durable yet flexible PCB structure. Thus the board becomes suitable for space constraints application, along with heavy components on the rigid sections.
6. HDI PCBs
Applications demanding higher performance than regular PCBs will opt for a HDI PCB. This board has a better layout, design and construction.
Layers of Flex PCB
In the PCB fabrication process, each layer plays a critical role in contributing to the board's impressive functionalities.
1. Conductive Layer
This layer is typically made of copper, which is softer and more malleable providing flexibility, essential for wearable technology.
2. Dielectric Substrate Layer
This layer provides the physical base for the conductive materials. It also serves as an electrical insulator in multi-layer configurations.
3. Adhesive Layer
In multilayer PCB assembly, adhesive is used to bind the substrate to the copper foil. In high-flex applications, adhesiveless base materials may be used to heighten the flexibility.
4. Coverlay
Made from flexible materials like polyimide films, coverlays protect the conductive circuits from environmental factors like dust, moisture, and mechanical abrasion.
5. Stiffeners
These layers are typically made from materials like FR4 or polyimide, depending on the needed support. They are used to reinforce areas where the PCB component is mounted or where additional rigidity is required.
Benefits and Disadvantages of Flexible Printed Circuit Boards
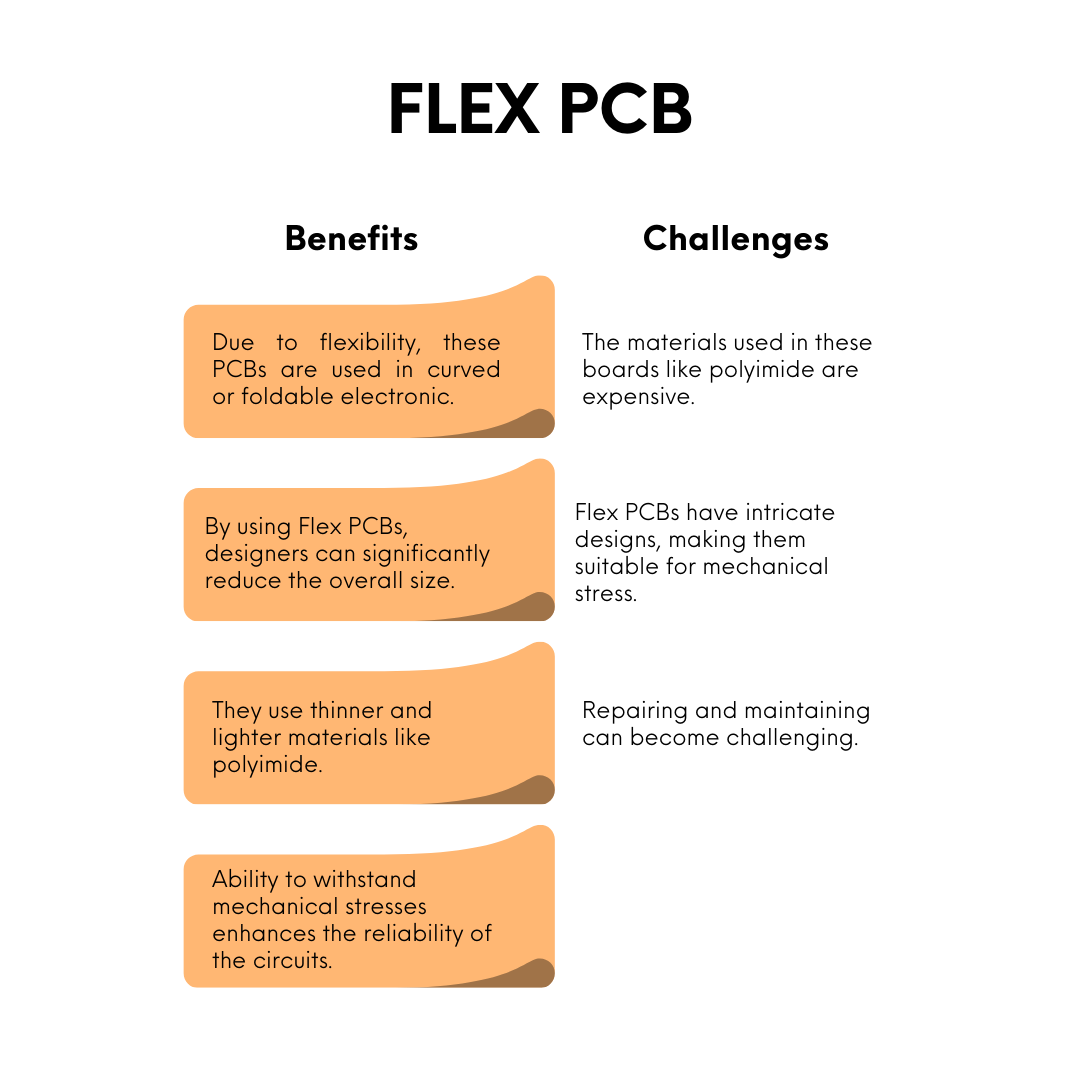
Flexible PCBs offer a wide range of benefits as compared to other boards. Here are some of them:
1. Flexibility:
Due to flexibility, these PCBs are used in curved or foldable electronics.
2. Space-Saving:
By using Flex PCBs, designers can significantly reduce the overall size of electronic devices.
3. Reduced Weight:
Flex PCBs are lighter because they use thinner and lighter materials like polyimide, which is crucial for aerospace and wearable technology.
4. Improved Reliability and Durability:
The ability to withstand mechanical stresses enhances the reliability and longevity of the circuits.
5. Enhanced Thermal Management:
Due to their thinness and the use of polyimide, Flex PCBs can withstand high temperatures. Even a Teflon PCB are known to sustain harsh environments.
Disadvantages of Flexible Printed Circuit Boards
While Flex PCBs offer significant advantages, they also have some drawbacks and challenges:
1. Higher Initial Cost:
The materials used in these boards like polyimide are expensive. Even the manufacturing process is also complex, adding to the production cost.
2. Complexity in Design:
Flex PCBs have intricate designs, making them suitable for mechanical stress and electrical functionality. Thus it requires specialised expertise.
3. Manufacturing and Repairing Challenges:
For their complex design, these boards require careful handling to avoid damage. Thus repairing and maintaining can become challenging.
Materials Used for Making Flexible PCB
The Flex PCB manufacturing process requires various materials depending on its components such as PCB stencil, PCB pad etc. However, here are some common materials to be used:
1. Polyimide
Polyimide is favoured for its high thermal stability (up to 400°C), flexibility, and chemical resistance. That’s why it is ideal for demanding applications such as aerospace or industrial technologies.
2. Polyester
Polyester is used where cost-efficiency is key. It offers sufficient flexibility and decent thermal resistance (up to 150°C) for consumer electronics. However, it's less robust than polyimide.
3. Adhesives
Acrylics and epoxy resins are used to bond layers together without compromising on flexibility. Adhesiveless options are also available.
Flex PCB Use Cases
Flex PCBs are widely used across various industries due to their unique properties.
Flexible Displays: In rollable displays, Flex PCBs are used due to their flexibility. They create bendable screens that can be rolled or folded, as seen in the latest smartphone and TV designs.
Smart Clothing: Flex PCBs are integrated into smart fabrics and clothing to monitor health metrics. It also measures the change in the garment's properties based on environmental changes.
Biomedical Sensors: Biomedical devices are increasingly using PCBs. They help in continuous health monitoring without the discomfort or limitations of rigid components. RF PCB can read radio signals which often work in this field.
Applications of Flex PCB
Flexible Printed Circuit Boards are widely accepted across various sectors due to their amazing properties.
1. Consumer Electronics
Since Flex PCBs support slimmer and lighter designs, popular everyday electronic devices such as smartphones, laptops, tablets, cameras, smartwatches and fitness trackers extensively use these boards. You can find Taconic PCB in microwaves, as it is known for low loss factors.
2. Automotive
In vehicles, Flex PCBs are used in lighting systems, infotainment systems, sensors etc. These boards protect the system from harsh conditions such as vibrations and temperature fluctuations, which are common in automotive environments.
3. Medical Devices
Medical devices such as pacemakers, portable medical monitoring devices, and advanced prosthetics are required to be lightweight. Flex PCBs provide reliability and comfort in such applications.
4. Aerospace
High-frequency PCB can be found in instruments, control systems, and interior lighting solutions in aircraft and spacecraft. Their durability to withstand extreme environmental conditions makes them ideal for aerospace applications.
5. Industrial
Flex PCBs show flexibility to fit into complex designs and durability in industrial environments making them suitable for robotics, control systems, sensors etc.
Structure of a Flexible PCB
But what exactly is the structure of Flex PCBs? Let’s break it down:
1. Dielectric Substrate Film
It is the foundation of the circuit board. Polyimide is generally used due to its high resistance power against mechanical stress and temperature.
2. Electrical Conductors
Then, there are electrical conductors. These conductors are made from copper, which is known for its excellent electrical conductivity.
3. Protective Finish
After that, there is a coverlay, which is applied as a protective finish. This layer works as an insulator, preventing electrical shorts.
4. Adhesive Material
Adhesive materials, such as polyethene or epoxy resin, are used to bond the layers of the circuit together.
Final Thoughts
In advanced technology, using Flex PCBs is very common. They are more diverse than traditional rigid PCBs. Be it durability or complicated applications Flex PCBs hold the ability to be suitable in all scenarios. However, there are issues like high maintenance, expensive etc. But there is no doubt that they are an ideal circuit board for consumer electronics, automotive applications, medical devices, and aerospace technology. Flex PCBs will be an ideal choice for companies working on any project that requires space-saving and lightweight components,